About
A prominent energy company in KSA, dedicated to exploring, developing, and producing oil and gas resources. The company operates with a focus on sustainability and innovation, ensuring that its operations align with the highest standards of environmental and social responsibility. This commitment positions the company as a leader in the global energy sector, continually striving to enhance efficiency and reduce environmental impact.
Scope
The project involved the Material Master Data Cleansing and Standardization of approximately 100,000 SKUs. This included:
- Enhancement of material specification data via web sourcing and physical verification.
- Classification of material master data.
- Codification using the UNSPSC logic.
Material Master Data Cleansing and Standardization was done for approximately 100,000 SKUs
The project was completed over a span of 10 months
Our Solution
To meet the client’s needs, we provided a comprehensive suite of services:
- Analyzing, cleansing, segregating, cataloguing, and creating a robust database for the Material Master.
- Conducting a physical audit of materials to ensure accurate and reliable data.
- Identifying and eliminating duplicate entries.
- Tracking and recording all data with respect to different statuses (new creation, clarification, existing code) and quantities.
- Linking images to each data entry for enhanced visual reference and verification.
- Establishing optimal levels for cost savings, finding the correct balance between risk and criticality levels.
- Implementing a quantitative evaluation methodology to suggest inventory control parameters.
- Developing a methodology to analyze risk pooling and correct duplicates that impact inventory costs.
Process
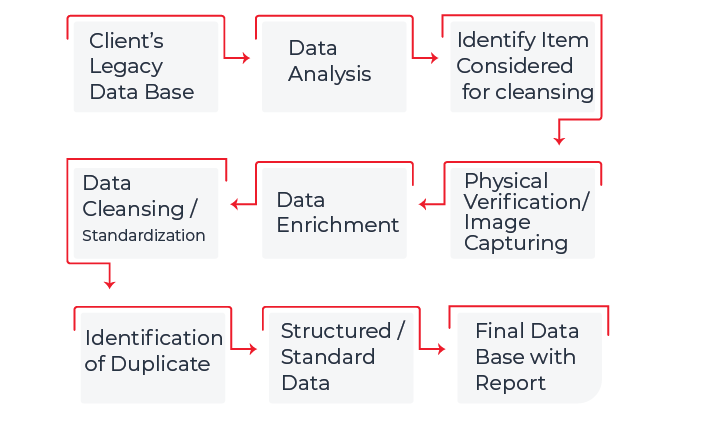
Outcome
The project provided the client with a cleansed, standardized, and enriched material master database, significantly enhancing data accuracy and operational efficiency.
Benefits
- Realized substantial cost savings by eliminating redundancies and optimizing inventory control parameters.
- Improved data quality, leading to better decision-making processes and reduced administrative costs.
- Streamlined workflows through optimized inventory levels and accurate material records, saving time and resources.
- Enhanced information access with structured data and linked images, facilitating coordination across various locations.
- Minimized excess stock and related costs through the implementation of optimal inventory control parameters.
- Reduced risks associated with inventory management by employing a methodology for risk pooling and duplicate correction.