Unplanned shutdown in the oil and gas industry lead to production delays, quality degradation, reputational loss, and diminishing customer support and trust. Moreover, the operational issues caused by the breakages impact significant losses and hold back profits. Here’s how Master Data Management (MDM) and preventive maintenance are transforming the industry by preventing unplanned downtime and saving up to $8.9M per incident.
What is an unplanned shutdown in the oil and gas industry?
Unplanned shutdown in the oil and gas industry are sudden interruptions or breakages in the production line due to equipment failures, system corruption, data mismanagement, spare parts shortages, electricity outages, natural disasters, and other unforeseen issues that emerge without any notice period. These halts need immediate responses to avoid costly mistakes and errors.
Causes of unplanned shutdowns in the oil and gas industry.
Equipment failure
Equipment failure may often occur due to the malfunction and aging criteria of the parts and machinery like pumps, compressors, turbines, and pipelines in the oil and gas industry. Additionally, sudden breakages of these materials are also caused by poor or lack of material maintenance.
Electricity outages
Sudden failures in both external and internal circuit breakers, generators, and transformers cause immediate power loss in the plant and consequently slow down the production, drilling, refining, or distribution processes, leading to delayed project timelines, revenue losses, and other operations.
Human error
Mismanagement of equipment and other mistakes by labor and manual operations can cause malfunctions, and improper maintenance practices can result in errors in repairs or overlooked safety procedures.
How does MDM act as a preventive measure to cut unplanned downtimes for the oil and gas industry?
Master Data Management (MDM) acts as a preventive measure in the oil and gas industry by ensuring the accuracy, consistency, and integrity of critical data across operations. Here’s how it helps prevent potential issues:
Reduces unplanned downtime
The consolidated and standardized data about equipment, spare parts, and inventories of the oil and gas industry ensure accurate data and correct missing parts and reduce the risk of equipment failures and unplanned downtime.
Regulatory Compliance
Critical industries like oil and gas depend heavily on regulatory compliance to avoid legal penalties. MDM ensures compliance-related data by handling ISSO certification standard data management.
Supports Operational efficiencies
The breakages of data silos in MDM prevent data errors caused by inconsistent and duplicate data and foster streamlined workflows from procurement and production to supply chain distribution to avoid bottlenecks caused by inaccurate data.
Predictive Maintenance
MDM enables predictive maintenance that closely tracks the IoT-integrated tools and equipment to gain real-time data insights to prevent unexpected breakdowns, identify wear and tear patterns, and spot potential issues before they escalate.
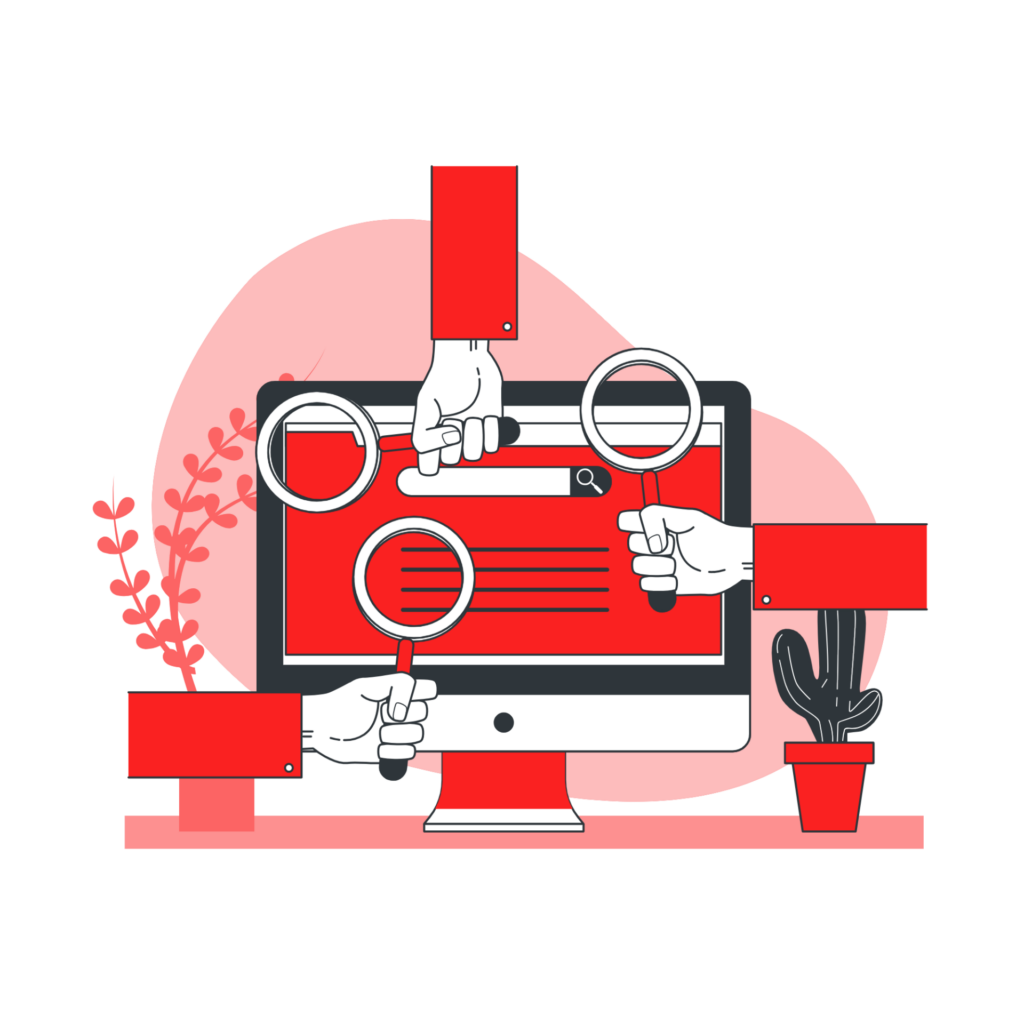
Are you ready to prevent unplanned downtimes?
Explore how Codasol’s tailored solutions optimize inventory and eliminate costly errors.
Predictive Maintenance Use Cases for the oil & gas industry to prevent unplanned shutdown
Pump Condition Monitoring
Predictive maintenance gains real-time data to track the gas pump’s flow, power, vibration, infrared thermography, oil analysis, and ultrasonic testing to check for any leakages. Data analysts run simulations by comparing past reports of pump conditions with real-time data to predict and alert the company before any escalation and potential failures.
Vessel Maintenance & Monitoring
Real-time data collection from vessel monitoring closely tracks the entire vessel operation, from its pressure to fluid’ temperature. The real-time data collection from predictive maintenance allows operators to identify any possible problems. This enables oil and gas companies to operate safely, efficiently, and with streamlined processes.
Tank Pressure Monitoring
IoT-enabled tank sensors with real-time monitoring using the help of predictive maintenance allow plant managers to track ullage (the gap between the top of the tank and the liquid surface), pressure, temperature, and discharging rate. This technology ensures worker safety while preserving the integrity of the tank’s contents.
Virtual Rig Monitoring
Traditionally, predictive maintenance is performed by monitoring real equipment in the actual place. With the advent of virtual rig monitoring, it can be carried out remotely. This enables oil and gas businesses to spot possible rig faults before they become a problem, ensuring that operations continue to function at peak efficiency.
Machinery Condition Monitoring System and Asset Protection
Oil drilling machinery has varying speeds, vibrations, and power. For instance, drilling thrusters vary their load and speed while mud pumps have complex vibration patterns that need to be identified and isolated from other equipment to track trends, check diagnostics, and trigger alerts when an issue arises. To address these challenges, Predictive maintenance software ensures optimal machinery conditions through real-time tracking and monitoring.
Plant Performance Monitoring
The combination of predictive analytics and data science examines the plant’s operational abnormalities, addresses the root cause of production bottlenecks, and automatically accesses failure modes in real time. IoT in the oil and gas industry enhances plant efficiency and improves availability.
IoT Pipeline Monitoring
Pipelines of crude oil and natural gas span for a long time and must be regularly monitored to ensure operational efficiency and personal safety. Damages or any other flaws in these pipelines lead to explosions, leakages, and other environmental harms. By leveraging IoT-censored devices, real-time monitoring reduces unplanned shutdowns and revenue losses.
Drill Corrosion Detection and Maintenance
Corrosion takes place when metal is subjected to electrochemical processes during drilling operations. Equipment made with corrosion resistance reduces damages. Therefore, adding corrosion-detecting sensors to drilling equipment can help with early identification and repairs.
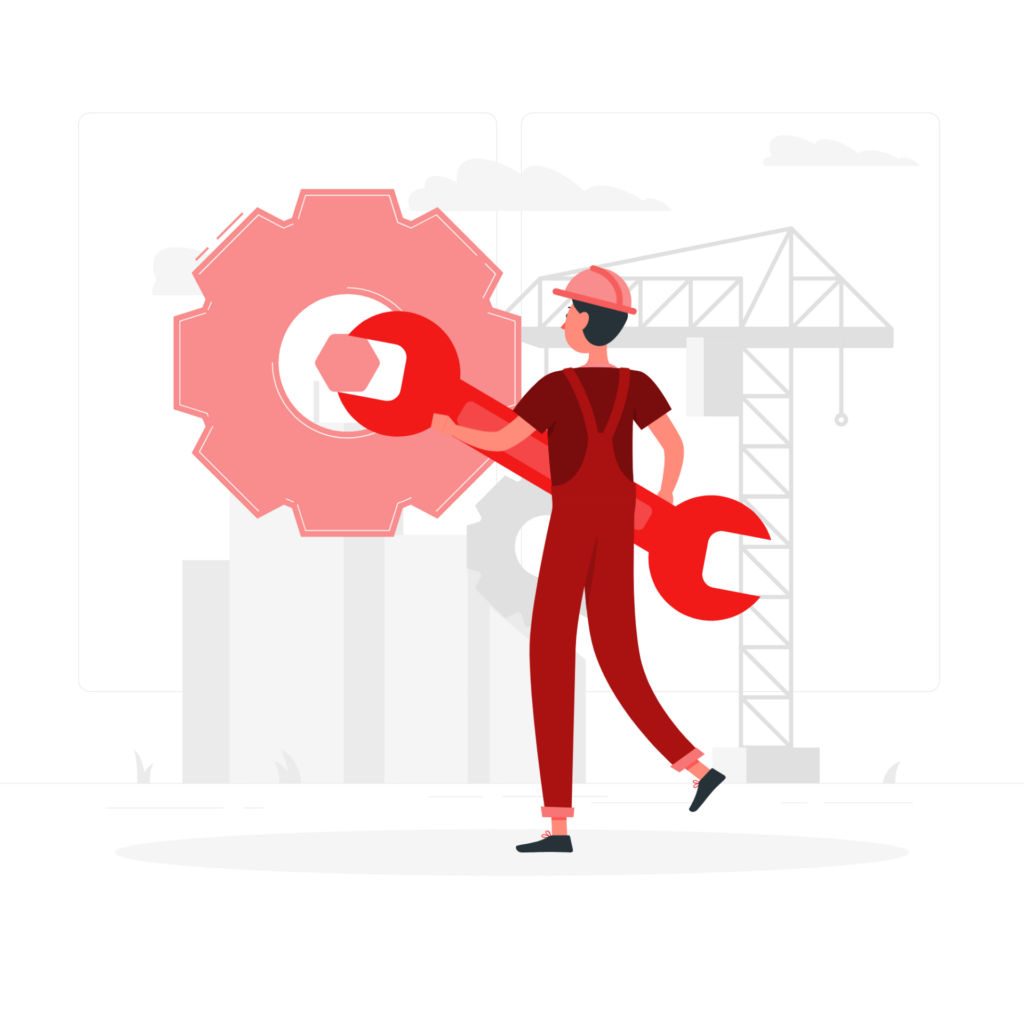
Discover how predictive maintenance and MDM can save millions in operational costs.
Streamline your operations today.
How Codasol prevents unplanned downtime with its cutting-edge solutions.
A major energy company in KSA focuses on exploring, developing, and producing oil and gas resources. Material Master Data cleansing and standardization were completed for approximately 100,000 SKUs over 10 months.
How we approach
To meet the client’s needs, we provided tailored solutions.
Building a Strong Foundation:
We analyzed, cleansed, and cataloged the Material Master Data to create a reliable and accurate database.
Ensuring Accuracy on the Ground:
A physical audit of materials was conducted to validate and enhance data reliability.
Eliminating Redundancy:
We identified and removed duplicate entries, ensuring a clean and streamlined dataset.
Enhancing Data Usability:
We provided enhanced visual references by linking images to data entries for easier identification and verification.
Optimizing Inventory Levels:
Through a detailed risk and criticality analysis, we established optimal inventory levels to drive cost savings.
Strengthening Inventory Management:
A quantitative evaluation methodology was implemented to define effective inventory control parameters.
Addressing Cost Drivers:
We developed a methodology to analyze risk pooling and correct duplicates impacting inventory costs.
The Process:
The Benefits
- Achieved significant cost savings by removing redundancies and optimizing inventory controls.
- Improved data quality for better decisions and lower administrative costs.
- Streamlined workflows, saving time and resources with accurate material records.
- Enhanced coordination through structured data and linked images.
- Minimized excess stock and costs with optimized inventory levels.
- Reduced inventory risks and duplicate correction methodologies.
Wrapping Thoughts
Unplanned shutdown in the oil and gas industry can result in significant financial losses and operational challenges. However, Master Data Management (MDM) presents a proactive solution to mitigate these risks. By ensuring data is accurate, consistent, and actionable, MDM enables companies to implement predictive maintenance, streamline workflows, and improve decision-making processes.
Codasol has a proven track record in transforming operations, exemplified by a successful 100,000 SKU Material Master Data project completed in just 10 months. This approach helps clients optimize inventory levels, eliminate redundancies, and reduce unplanned downtimes, ultimately saving them up to $8.9 million in return on investment (ROI).
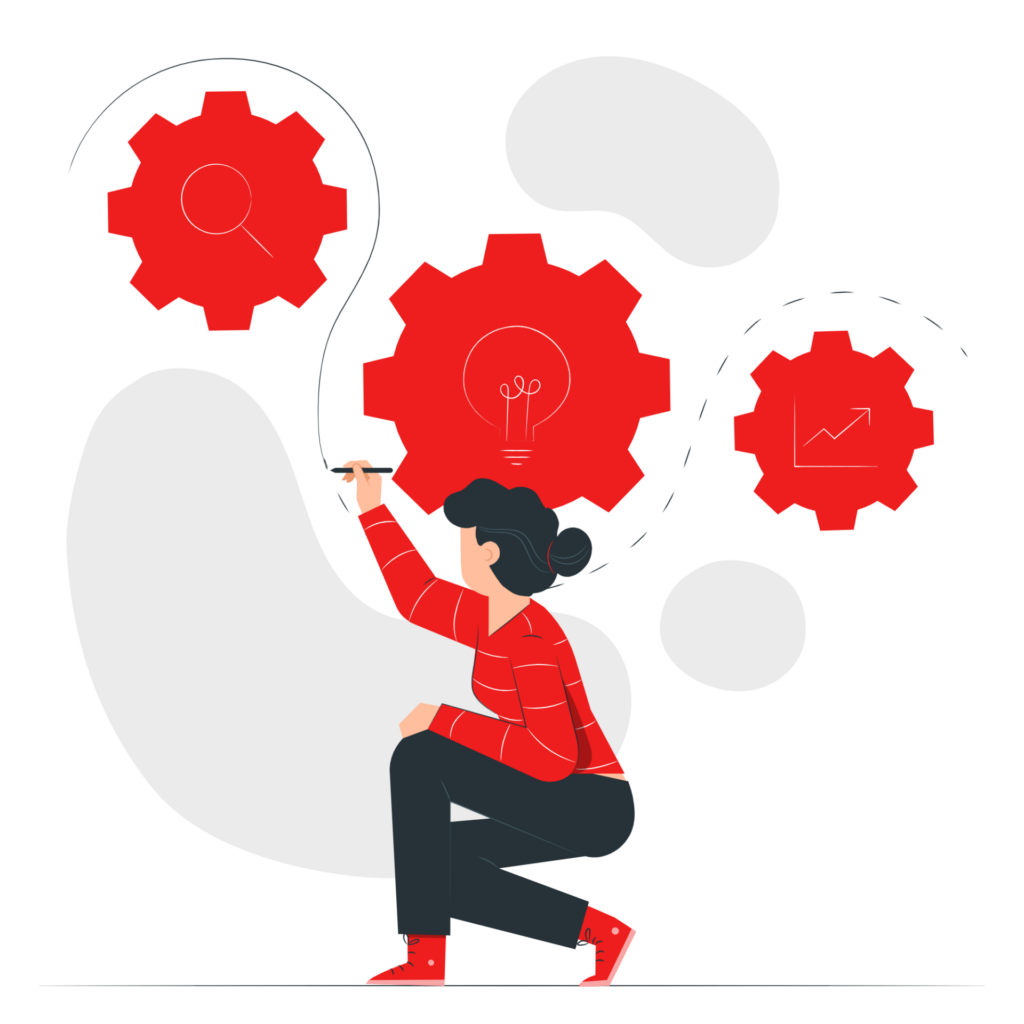
Contact Codasol now to ensure operational excellence and make data work for you.