Why MRO Data Matters More Than Ever
Maintenance, Repair, and Operations (MRO) data is the backbone of industrial efficiency. But without proper MRO data cleansing and enrichment, businesses face duplicate inventory, procurement inefficiencies, and system failures. Poor MRO data quality can cost companies millions in wasted resources, delays, and excess inventory.
With data-driven decision-making becoming a competitive advantage, industries must prioritize MRO data cleansing and enrichment to enhance their ERP (Enterprise Resource Planning) and EAM (Enterprise Asset Management) systems.
Key Takeaways:
- Learn how MRO data cleansing and enrichment solve procurement and maintenance challenges.
- Discover real-world case studies of companies reducing costs with data optimization.
- Understand how AI & automation can transform your material master data management.
The Cost of Poor MRO Data Quality
1. Duplicate and Inaccurate Data Lead to Inventory Bloat
Duplicate and inaccurate MRO data results in excess inventory, costing companies millions. A recent case study on material master data cleansing revealed:
- 12% of materials were duplicates, causing unnecessary purchases.
- $3.36 million in potential savings by eliminating redundant inventory.
Example: A steel manufacturing company had 100,000 MRO materials listed. After data cleansing, they reduced their unique items to 12,000, optimizing procurement and storage.
2. Increased Procurement Costs Due to Poor Data Classification
Misclassified materials cause erroneous procurement, leading to unnecessary spending. Without standardized MRO data, procurement teams unknowingly reorder duplicate items, driving up costs.
Solution: Standardized material categorization in ERP and consistent taxonomy using AI-driven MRO data cleansing tools.
3. Unplanned Downtime & Maintenance Delays
Poor MRO data quality disrupts operations. Technicians waste time searching for the right spare parts, leading to delayed maintenance and unplanned downtime.
💡 Impact: In a large offshore oil platform, an MRO data issue caused a 12-hour shutdown, resulting in:
- $8.4 million lost revenue
- $500,000 turnaround costs
- Total impact: $8.9 million
Fix: Enriched data ensures accurate descriptions, manufacturer details, and linked BOMs (Bill of Materials), helping technicians quickly locate parts.
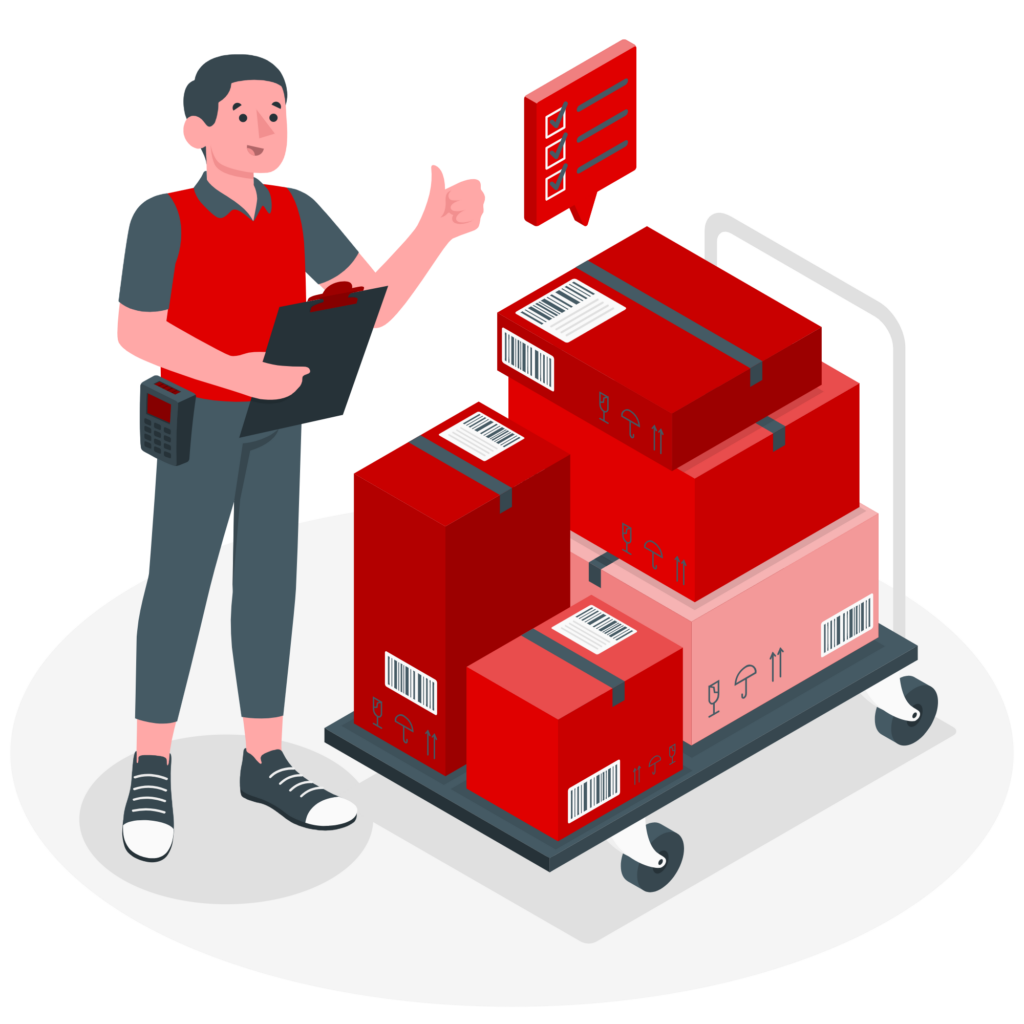
Ready to optimize your Inventory?
What is MRO Data Cleansing?
MRO data cleansing is the process of identifying, correcting, and standardizing material master data to improve data integrity.
Key Steps in MRO Data Cleansing:
- De-duplication – Identifying and merging duplicate records.
- Standardization – Ensuring uniform naming conventions and attributes.
- Normalization – Correcting inconsistent formats across different systems.
- Validation – Cross-referencing data with OEM specifications and industry standards.
- Error Correction – Fixing incorrect part descriptions and misclassified materials.
Example: After data cleansing, a major petrochemical plant optimized 40% of its MRO inventory, saving millions in procurement costs.
What is MRO Data Enrichment?
MRO data enrichment enhances material master records by adding missing data, linking to supplier catalogs, and ensuring detailed part descriptions.
Key Steps in MRO Data Enrichment:
- Adding Technical Specifications – Complete descriptions for easy identification.
- OEM & Supplier Data Linking – Ensuring compatibility and authenticity.
- Image & Datasheet Attachment – Visual references for maintenance teams.
- Taxonomy & Classification Enhancement – Using UNSPSC, eCl@ss, or ISO 8000 standards.
- Integration with ERP & EAM Systems – Real-time data synchronization.
Case Study:
A global fertilizer company enriched its MRO database, linking OEM part numbers with correct manufacturer names. Result:
- Reduced procurement cycle time by 50%
- Decreased stockouts and emergency purchases
Business Benefits of MRO Data Cleansing & Enrichment
Why Invest in MRO Data Management?
- Reduce Procurement Costs – Avoid duplicate purchases and optimize spending.
- Improve Maintenance Efficiency – Faster part identification minimizes downtime.
- Enhance ERP/EAM Performance – Structured data enables seamless integration.
- Optimize Inventory Levels – Prevent overstocking and reduce working capital.
Example: One manufacturer reduced its MRO inventory by 20%, freeing up $5 million in tied-up capital.
Best Practices for MRO Data Cleansing & Enrichment
To maximize efficiency, follow these best practices:
1. Conduct Regular Data Audits
Routine MRO data audits identify and fix errors before they impact operations.
2. Leverage AI & Automation for Data Cleansing
AI-driven MRO data cleansing tools detect duplicates and inconsistencies in real time.
3. Implement Industry Standards
Standardized material classification (UNSPSC, eCl@ss, ISO 14224) ensures consistency.
4. Train Teams on MRO Data Management
Empower your procurement and maintenance teams with data governance training.
5. Integrate with ERP & CMMS Systems
Ensure clean MRO data syncs with your SAP, Oracle, or Maximo systems.
How AI & Machine Learning Transform MRO Data Management
AI and ML improve MRO data management by:
- Automating data deduplication
- Enhancing real-time anomaly detection
- Classifying materials with NLP (Natural Language Processing)
- Predicting spare part demand trends
Example:
A global cement manufacturer used AI-powered data cleansing, reducing material search time by 70%.
Case Studies:
📊 Case Study 1: Material Master Data Cleansing & Standardization
- Challenge: Excessive duplicates and poor classification.
- Solution: AI-powered data standardization.
- Results:
- 15% reduction in procurement spending
- 30% faster spare part retrieval
Read more: https://www.codasol.com/material-master-data-cleansing-and-standardization/
📊 Case Study 2: Data Cleansing & Enrichment in MRO Inventory
- Challenge: Unstructured, outdated ERP data.
- Solution: Automated data enrichment linking supplier data.
- Results:
- 20% inventory reduction
- 40% faster procurement cycle
Conclusion:
MRO data cleansing and enrichment are essential for cost savings, efficiency, and seamless ERP/EAM integration. By leveraging AI-powered solutions, companies can achieve:
- Reduced procurement costs
- Optimized inventory levels
- Enhanced maintenance efficiency
Transform Your MRO Data Today
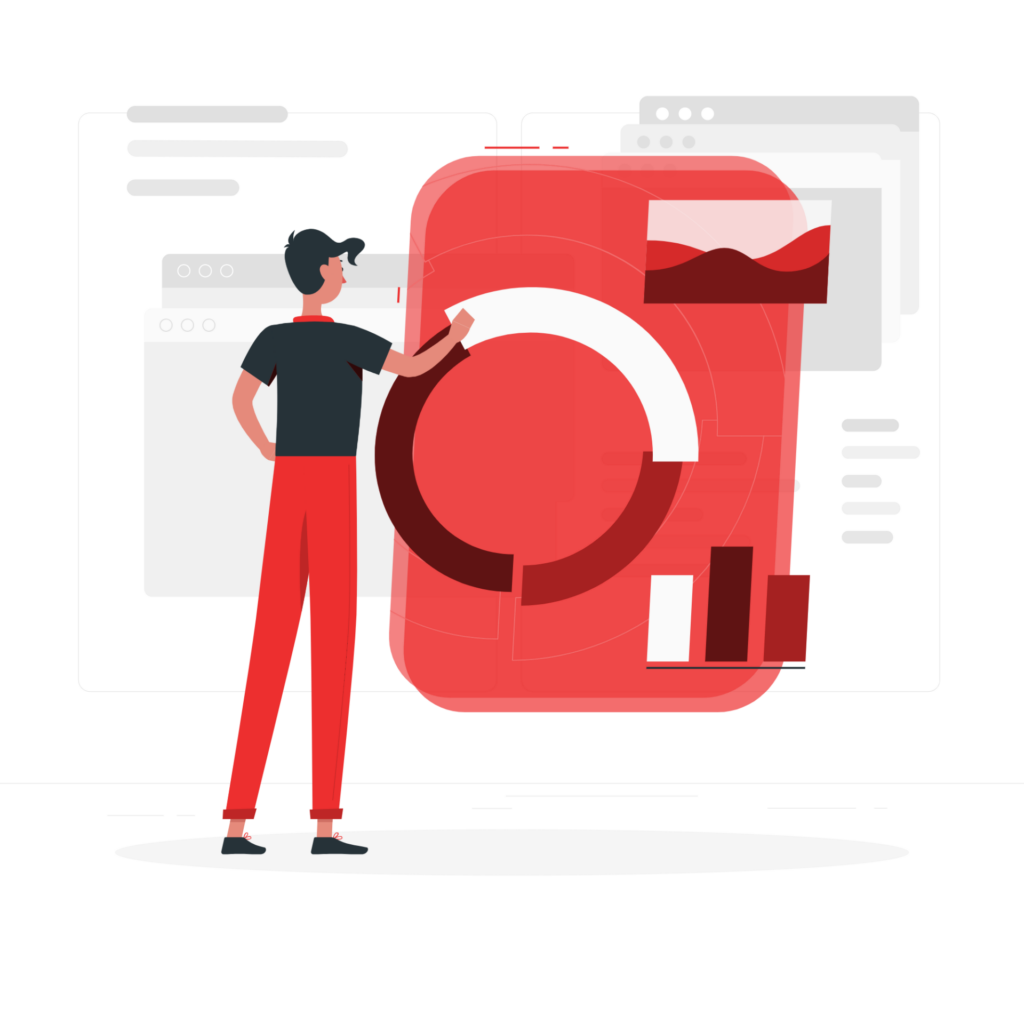
📌 Further Reading: