Choosing the right maintenance strategy can significantly impact your operational efficiency, costs, and equipment lifespan. When comparing Reactive vs. Preventive vs. Predictive Maintenance, it’s essential to understand how each approach works, and which one aligns best with your business goals.
While reactive maintenance deals with fixing failures as they occur, preventive maintenance focuses on scheduled servicing to avoid breakdowns, and predictive maintenance leverages data and AI to anticipate issues before they happen.
But which one is right for you? Let’s break it down. This guide will help you weigh the pros, cons, real-world applications, and success stories to help you choose the right approach.
Reactive Maintenance: Fixing Equipment After Failure
What is Reactive Maintenance?
- Also called run-to-failure maintenance, this strategy involves repairing equipment only after it breaks down.
- It requires no proactive monitoring or servicing and is the simplest approach.
Advantages of Reactive Maintenance
- Low upfront costs – No need for predictive tools or scheduled servicing.
- Simple execution – No planning or resources required until failure occurs.
- Best for non-critical assets – Ideal when downtime has minimal impact.
Disadvantages of Reactive Maintenance
- High long-term costs – Emergency repairs, overtime labor, and expedited shipping increase expenses.
- Increased downtime – Breakdowns lead to production delays and potential revenue loss.
- Safety & compliance risks – Equipment failure can result in workplace hazards or regulatory penalties.
When to Use Reactive Maintenance
- When equipment failure has minimal operational impact.
- For non-critical or low-cost machinery that is easy to replace.
- When budget constraints limit investment in proactive maintenance.
Case Study: Data Cleansing & De-duplication
A manufacturing company struggled with inaccurate and duplicate material records, leading to delays in sourcing spare parts during equipment failures. CODASOL’s data cleansing and de-duplication services streamlined their material master data, reducing procurement delays and improving maintenance response times. While reactive maintenance still played a role, having accurate data minimized downtime and improved decision-making.
Read the full case study:
Preventive Maintenance: Scheduled Servicing to Avoid Failures
What is Preventive Maintenance?
- Involves regular inspections, servicing, and part replacements based on time intervals or usage cycles.
- Uses historical data, OEM recommendations, and industry standards to schedule maintenance.
Advantages of Preventive Maintenance
- Reduces unplanned downtime – Prevents unexpected failures and disruptions.
- Extends asset lifespan – Regular servicing enhances performance.
- Cost-effective long-term – Saves on emergency repairs and replacements.
- Improves workplace safety – Minimizes risks of sudden equipment failures.
Disadvantages of Preventive Maintenance
- Higher initial costs – Requires routine inspections, spare parts, and scheduled downtime.
- Inefficient for low-risk assets – Some servicing may be unnecessary if equipment is still in good condition.
- Resource-intensive – Needs skilled manpower and tracking systems.
When to Use Preventive Maintenance
- When unplanned downtime would result in major revenue loss.
- For critical machinery in manufacturing, energy, and oil & gas industries.
- When equipment follows a predictable wear-and-tear cycle.
Case Study: BOM Creation and Preventive Maintenance (PM) Plan in SAP
A chemical industry leader needed a robust preventive maintenance strategy but lacked standardized asset and BOM (Bill of Materials) data. CODASOL implemented BOM creation and PM plan development in SAP, ensuring scheduled maintenance tasks were aligned with asset lifecycles. This led to a significant reduction in equipment failures and optimized maintenance planning.
Read the full case study:
Case Study: Asset Registry Project
A leading utility company faced challenges tracking maintenance activities due to an unstructured asset registry. By implementing a comprehensive asset registry project, CODASOL enabled better asset visibility and preventive maintenance planning, reducing unplanned failures and extending equipment life.
Read the full case study:
Predictive Maintenance: Using Data & AI to Prevent Failures
What is Predictive Maintenance?
- Uses IoT sensors, AI-driven analytics, and real-time monitoring to predict equipment failures before they occur.
- Relies on machine learning algorithms to analyze patterns and detect early signs of failure.
Advantages of Predictive Maintenance
- Minimizes downtime – Repairs happen before critical failures.
- Reduces maintenance costs – Only necessary repairs are performed.
- Increases asset lifespan – Data-driven servicing optimizes performance.
- Enhances safety & compliance – Detects potential hazards in advance.
Disadvantages of Predictive Maintenance
- High upfront investment – Requires advanced sensors, analytics, and skilled personnel.
- Complex implementation – Needs integration with ERP and asset management systems.
- Requires continuous monitoring – Data accuracy is crucial for effective results.
When to Use Predictive Maintenance
- For high-value assets where failures are expensive.
- When real-time monitoring and IoT integration are available.
- In regulated industries where unplanned downtime leads to compliance issues.
Case Study: Coding & Cataloguing, BOM, and Data Analytics Using AI/ML
A company looking to shift from preventive to predictive maintenance struggled with inconsistent data structures. CODASOL provided AI/ML-driven coding and cataloging solutions, improving BOM accuracy and enabling predictive analytics for asset health monitoring. As a result, the company reduced maintenance costs and improved uptime by proactively addressing potential failures.
Read the full case study:
Optimize Your Maintenance Strategy with Expert Solutions
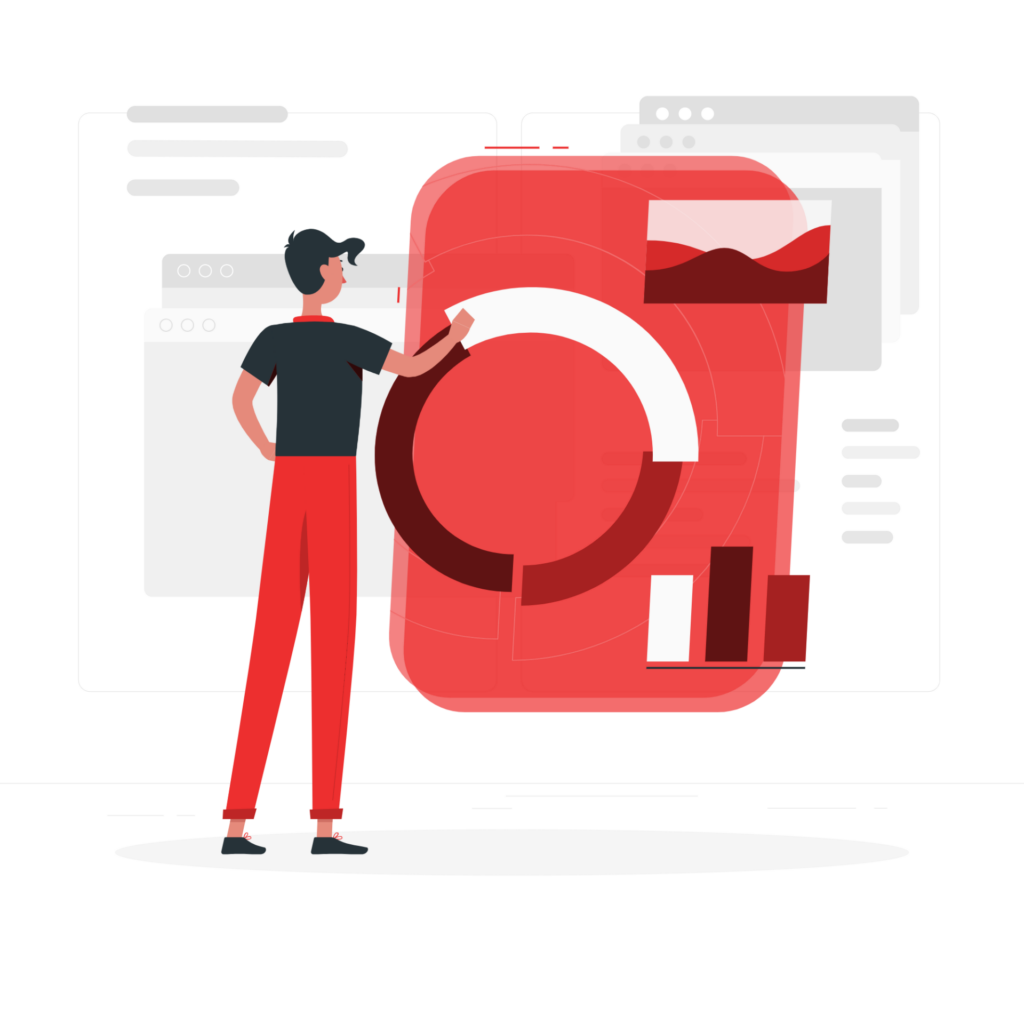
Struggling with unplanned downtime and high maintenance costs? Discover how data-driven maintenance strategies can improve efficiency.
Case Study: Material Data Management in SAP S/4HANA
A global enterprise transitioning to SAP S/4HANA needed clean material data to support predictive maintenance initiatives. CODASOL’s material data management solutions ensured accurate, standardized data, allowing the company to leverage AI-driven insights for maintenance forecasting and inventory optimization.
Read the full case study:
Comparison: Reactive vs. Preventive vs. Predictive Maintenance
Factor | Reactive Maintenance | Preventive Maintenance | Predictive Maintenance |
---|---|---|---|
Cost | Low upfront, high long-term | Medium upfront, cost-effective long-term | High upfront, very cost-efficient |
Downtime | High (unexpected failures) | Medium (scheduled servicing) | Low (optimized timing) |
Asset Lifespan | Shorter (runs to failure) | Longer (regular maintenance) | Longest (data-driven care) |
Ideal For | Non-critical assets | Most industrial settings | High-value or critical assets |
Technology Required | None | Basic scheduling software | IoT sensors, AI, ML |
How to Choose the Right Maintenance Strategy
- Evaluate equipment criticality – High-value assets benefit from predictive maintenance, while non-essential assets may use reactive strategies.
- Assess downtime impact – If downtime leads to lost revenue, preventive or predictive maintenance is essential.
- Consider budget constraints – Preventive maintenance has a moderate cost, while predictive maintenance requires a higher investment.
- Industry regulations – Predictive maintenance is often required in highly regulated industries like oil & gas and pharmaceuticals.
Learn More About Data-Driven Maintenance Strategies
Get expert insights on maintenance optimization and industry best practices.
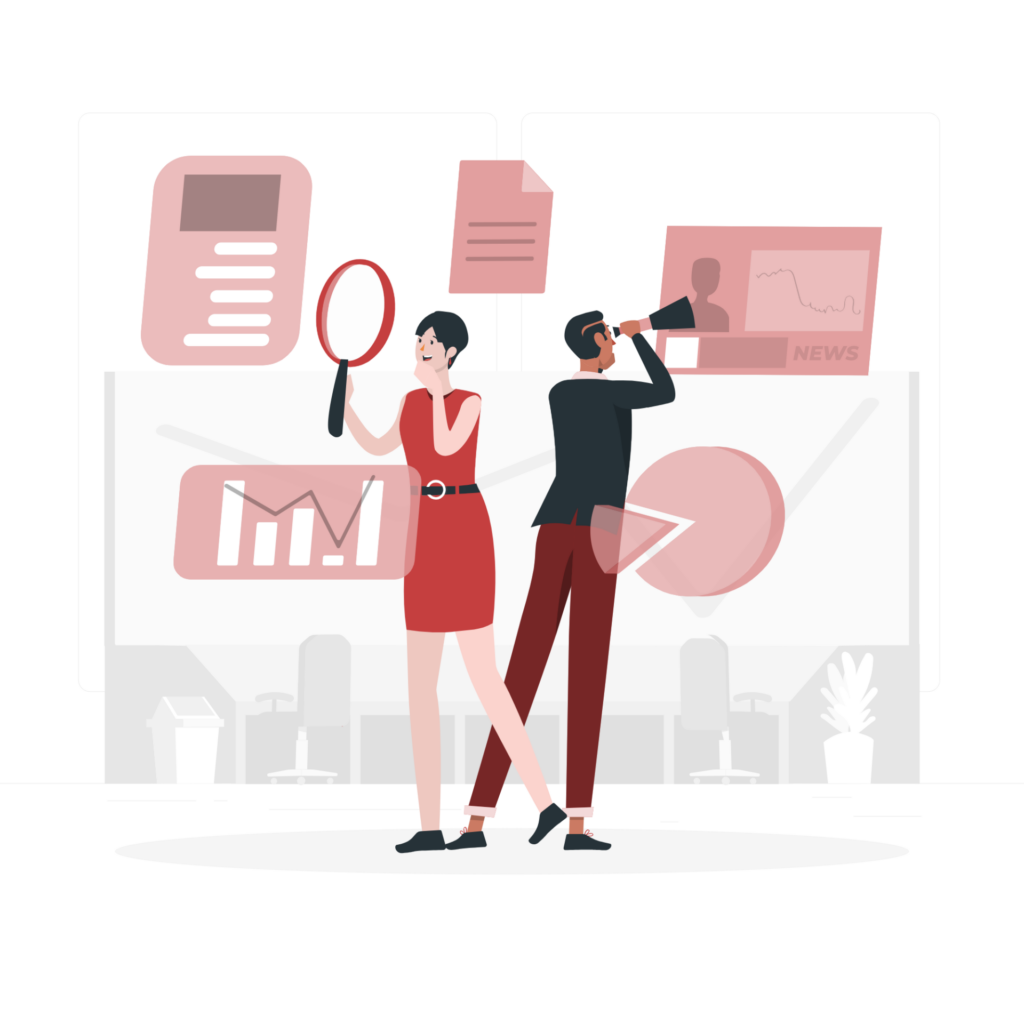
Key Takeaway:
Choosing between Reactive vs. Preventive vs. Predictive Maintenance depends on your business goals, asset criticality, and budget. While reactive maintenance is cost-effective upfront, it leads to higher downtime costs. Preventive maintenance balances cost and efficiency by scheduling regular servicing. Predictive maintenance, powered by IoT and AI, minimizes failures but requires significant investment. A hybrid approach often delivers the best results, ensuring reliability and cost savings.