Manufacturers today operate in highly complex environments where data accuracy plays a crucial role in decision-making, inventory control, and procurement efficiency. However, data inconsistency, duplication, and poor cataloguing often lead to operational inefficiencies, increased costs, and supply chain disruptions. A Master Data Cataloguing Tool, such as PROSOL, can solve these challenges by providing structured, standardized, and enriched material master data. By implementing such a tool, manufacturers can eliminate redundant materials, optimize inventory, and seamlessly integrate with ERP systems like SAP, Oracle, and Maximo.
In this blog post, we will explore the importance of a Master Data Cataloguing Tool, how PROSOL stands out, and why manufacturers must adopt it to ensure efficiency, cost savings, and supply chain resilience.
What is Master Data Cataloguing?
Master Data Cataloguing is the systematic process of organizing, standardizing, and enriching critical data assets like materials, spare parts, and equipment. It ensures that manufacturers have a single source of truth, preventing errors caused by inconsistent, outdated, or duplicate data.
Key Features of a Master Data Cataloguing Tool:
1. Data Deduplication & Cleansing:
Eliminates redundant entries to prevent overstocking.
2. Standardization & Classification:
Aligns data with international standards like ISO 8000.
3. ERP Integration:
Seamlessly connects with SAP, Oracle, and Maximo.
4. AI-Driven Data Enrichment:
Enhances data accuracy using machine learning algorithms.
5. Governance & Compliance:
Ensures adherence to industry regulations.
6. Real-Time Reporting & Analytics:
Provides data insights for smarter decision-making.
Without a structured Master Data Management solution, manufacturers suffer from procurement inefficiencies, supply chain disruptions, and inaccurate reporting.
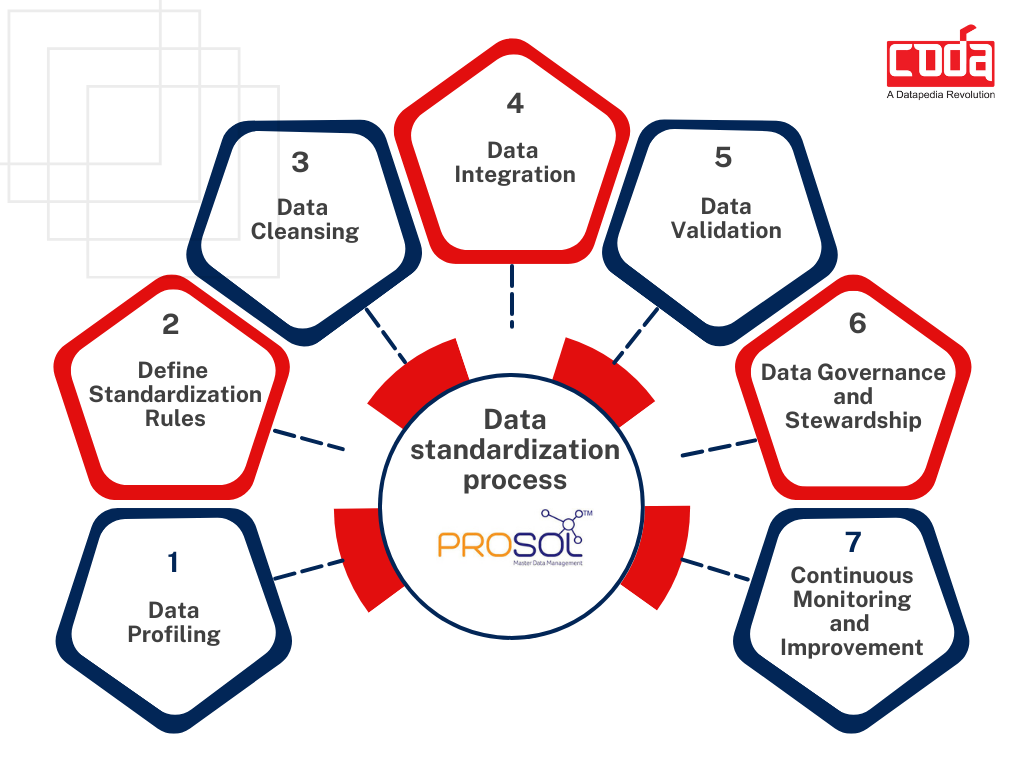
The Cost of Poor Master Data Management
Manufacturers dealing with inconsistent or duplicate data face severe financial and operational consequences:
- Duplicate materials inflate inventory costs unnecessarily.
- Inaccurate data leads to procurement delays and wrong purchases.
- Compliance risks arise from missing or incorrect specifications.
- Supply chain inefficiencies cause unplanned downtimes and disruptions.
Example:
A leading steel manufacturer discovered that 12% of its spare parts inventory was duplicate materials, leading to an avoidable cost of $3.4 million annually.
To address these challenges, manufacturers must implement Prosol’s Master Data Cataloguing Tool, designed to eliminate inefficiencies and optimize data governance.
For a deeper dive into these challenges, refer to Codasol’s blog post on the Top 8 Challenges in Implementing Master Data Management.
The Role of MDM in Supply Chain Management
Master Data Management plays a crucial role in supply chain efficiency:
- Accurate Inventory Management: MDM ensures precise inventory levels, reducing excess stock.
- Enhanced Transparency: Centralized data provides a clear overview of the supply chain.
- Sustainability: MDM supports effective crisis management and data governance.
For more insights, see Codasol’s blog on Master Data Management in Supply Chain.
Case Study
1. NATO Codification: Ensuring Compliance with Global Standards
Client Background
A leading defense contractor supplying equipment and spare parts to global military organizations needed to comply with the NATO Codification System (NCS). Their existing material master data lacked standardized descriptions, proper categorization, and compliance with NATO regulations, causing delays in procurement and supply chain operations.
Challenges Faced
- Inconsistent data formatting across multiple databases
- Duplicate material records, leading to procurement inefficiencies
- Lack of proper NATO Stock Numbers (NSN), affecting global trade compliance
Solution: Implementation of PROSOL
- Automated NATO Codification: PROSOL applied AI-driven cataloguing techniques to assign accurate NSNs to materials.
- Standardized Material Data: The tool restructured 40,000+ material records to meet NATO compliance.
- Duplicate Removal & Data Cleansing: Eliminated 15% redundant entries, streamlining inventory.
Results
- Reduced procurement delays by 35%
- Improved regulatory compliance, preventing trade restrictions
- Enhanced inventory visibility across international military supply chains
With PROSOL, the client achieved 100% NATO compliance, enabling seamless integration into global defense supply networks.
Read more: https://www.codasol.com/nato-codification/
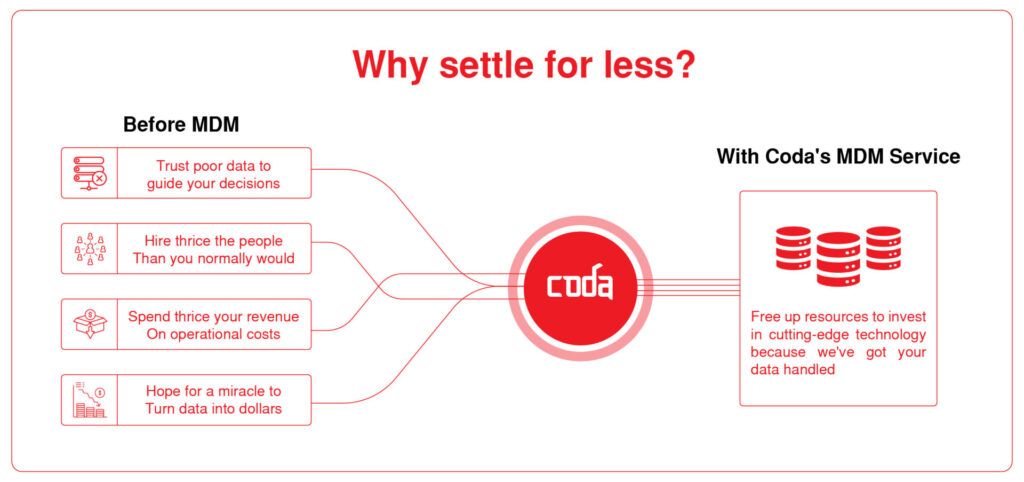
2. Material & Vendor Master Creation:
Client Background
A global automotive parts manufacturer faced challenges with vendor and material master data management. The company had multiple vendor entries for the same suppliers, leading to confusion, duplicate payments, and inefficiencies in procurement.
Challenges Faced
- Duplicate vendor and material entries, increasing procurement costs
- Inconsistent vendor naming conventions, causing data mismatches
- Lack of visibility into vendor performance, affecting supplier negotiations
Solution: PROSOL’s Vendor & Material Master Creation
- Consolidated Vendor Records: Merged multiple supplier entries into a single, standardized record.
- AI-Driven Material Data Cleansing: Identified and removed duplicate materials.
- Supplier Performance Analytics: Provided real-time insights into vendor performance.
Results
- Saved $2M annually by preventing duplicate payments
- Reduced procurement cycle time by 40%
- Improved supplier collaboration and contract negotiations
By using PROSOL, the manufacturer established a single source of truth for vendor and material data, optimizing procurement operations.
Read more: https://www.codasol.com/material-and-vendor-master-creation-case-study/
3. Material Data Standardization:
Client Background
A leading cement manufacturer struggled with unstructured material master data, leading to procurement inefficiencies and excess inventory. The company had inconsistent descriptions for materials, making it difficult for ERP systems to function properly.
Challenges Faced
- Material descriptions varied across locations, causing miscommunication
- Stock imbalances, leading to frequent stockouts and overstocking
- Inefficiencies in procurement due to ambiguous material records
Solution: PROSOL’s Standardization Framework
- AI-Driven Data Structuring: Applied standardized naming conventions across 100,000+ material records.
- Material Categorization & Classification: Enabled better inventory tracking and planning.
- ERP Integration: Ensured seamless data consistency across SAP and Oracle ERP systems.
Results
- Reduced excess inventory by 22%, saving $5M annually
- Eliminated inconsistencies in material descriptions across global locations
- Improved procurement accuracy, reducing supply chain disruptions
With PROSOL, the client streamlined material data governance, improving procurement efficiency and cost savings.
Read more: https://www.codasol.com/material-data-standardization-case-study-supplychain/
4. Coding & Cataloguing, BOM & Data Analytics using AI/ML
Client Background
A heavy machinery manufacturer needed to automate its master data cataloguing process, including BOM (Bill of Materials) management. The company struggled with manual data entry, inconsistencies, and poor visibility into component usage.
Challenges Faced
- Manual cataloguing process, leading to slow data entry and errors
- Inconsistent BOM structures, causing production delays
- Limited visibility into part replacements, increasing downtime
Solution: PROSOL’s AI/ML-Driven Automation
- Automated Material Coding & Cataloguing: AI algorithms classified and structured materials accurately.
- BOM Optimization: Standardized and enriched BOM records, reducing inconsistencies.
- Predictive Data Analytics: Used AI-driven insights to optimize spare parts procurement.
Results
- Reduced BOM errors by 30%, ensuring accurate production planning
- Improved spare parts forecasting, reducing unplanned downtime
- Increased operational efficiency, streamlining inventory management
By leveraging PROSOL’s AI/ML-driven cataloguing and analytics, the manufacturer optimized data accuracy, production efficiency, and cost savings.
Read more: https://www.codasol.com/coding-amp-cataloguing-bom-and-data-analytics-using-ai-ml/
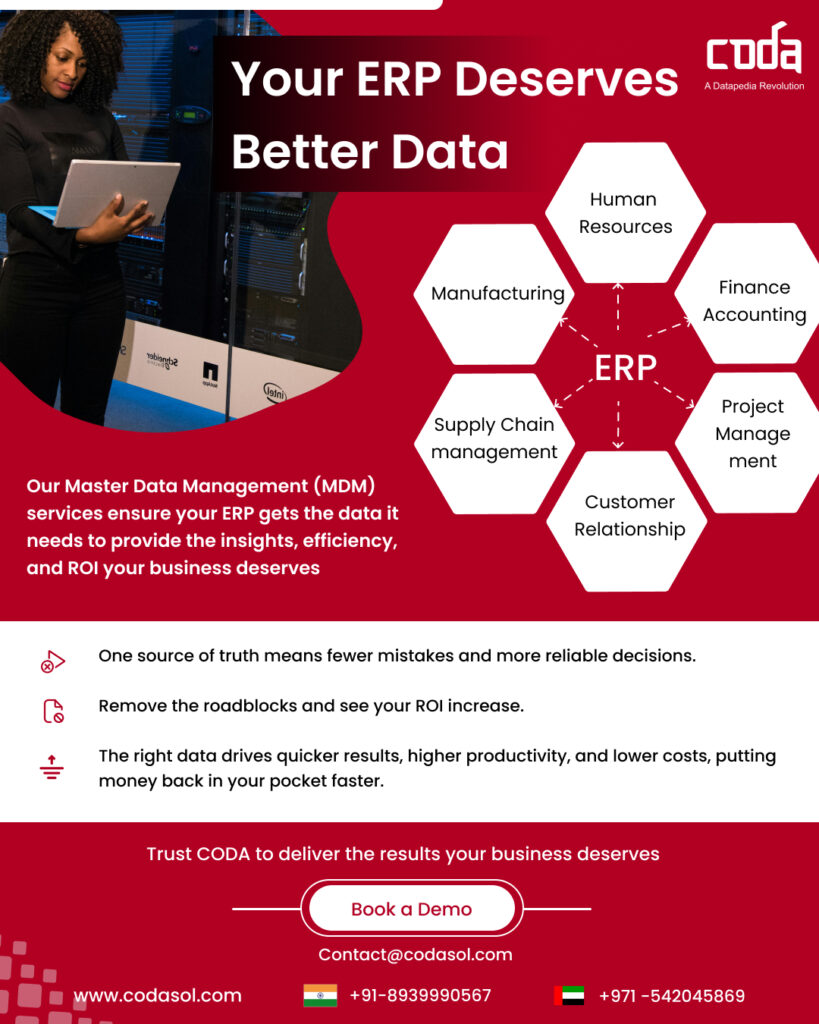
Comparison: Prosol vs. Other Master Data Cataloguing Tools
Feature | Prosol | Boomi | MDO Fuse | Informatica MDM | Pilog |
AI-Driven Data Deduplication | Yes | No | No | Yes | No |
Real-Time ERP Integration | Yes | Yes | Yes | Yes | Yes |
Compliance with ISO 8000 | Yes | No | Yes | Yes | Yes |
Predictive Analytics | Yes | No | No | Yes | No |
Customizable Workflows | Yes | Yes | No | Yes | Yes |
Automated Data Enrichment | Yes | No | Yes | Yes | No |
Advanced Reporting & Insights | Yes | Yes | No | Yes | No |
Prosol stands out with its AI-powered capabilities, predictive analytics, and industry compliance, making it the ideal choice for manufacturers.
Why Manufacturers Need Prosol
Prosol is the leading AI-powered Master Data Cataloguing Tool designed specifically for the manufacturing industry. It offers:
- Automated Data Cleansing & Deduplication – Eliminates redundancies to optimize inventory.
- Standardization & Enrichment – Ensures consistency with global industry standards.
- Seamless ERP Integration – Works with SAP, Oracle, Maximo, and more.
- Advanced Data Governance – Meets ISO, ASTM, and industry compliance requirements.
- AI-Powered Insights & Reporting – Enables smarter procurement and supply chain decisions.
With Prosol, manufacturers gain full control over their master data, ensuring efficiency, accuracy, and cost savings.
To know more about Prosol:
FAQs
1. How does PROSOL help with duplicate data removal?
PROSOL uses AI-powered algorithms to detect duplicate entries across multiple systems and automatically consolidates or removes them.
2. Is PROSOL compatible with all ERP systems?
Yes, PROSOL integrates seamlessly with SAP, Oracle, Maximo, and other ERP systems, ensuring smooth data flow.
3. What is the ROI of implementing a master data cataloguing tool?
Manufacturers using PROSOL typically see ROI within 6 months, with savings from reduced procurement costs, optimized inventory, and streamlined operations.
4. How long does it take to implement PROSOL?
Implementation time varies, but most manufacturers complete full deployment within 3-6 months.
5. Can small and mid-sized manufacturers use PROSOL?
Absolutely! PROSOL is scalable and can be tailored to the needs of small, mid-sized, and large enterprises.
Ready to Transform Your Master Data?
Don’t let poor data management cost you millions. Discover how Prosol can optimize your master data and enhance your bottom line.
By implementing a robust Master Data Cataloguing Tool, manufacturers can ensure data accuracy, operational efficiency, and long-term success.
Optimize your data. Transform your business. Choose Prosol.