Material master data is the backbone of procurement, maintenance, and inventory management. Yet, many companies suffer from inaccurate, duplicate, or incomplete material records, leading to inflated procurement costs, unplanned downtime, and inefficiencies across operations.
Why Is This Important?
Poor material master data can lead to:
- 15-20% excess inventory due to duplicate or misclassified items
- 70% of procurement errors stem from poor data quality.
- 40% of maintenance delays occur due to incorrect or missing spare part information.
- Higher procurement costs from rushed or incorrect purchases
- Frequent equipment failures due to missing or incorrect spare parts
- ERP inefficiencies, slowing down operations and reporting
- Companies lose millions annually due to inefficient inventory management.
This blog explores the real impact of poor material master data on procurement and maintenance costs, presents two case studies, and provides actionable solutions to fix these issues.
The Impact of Poor Material Master Data
1. Increased Procurement Costs
One of the biggest issues with poor material data is its impact on procurement operations. When duplicate, outdated, or inaccurate material records exist, it results in:
Duplicate Purchases – Lack of visibility into existing inventory leads to unnecessary purchases, increasing procurement costs.
(Learn more about the importance of Master Data Cleansing vs. Data Quality Management here)
Overstocking & Stockouts – Misclassified materials lead to inaccurate demand forecasting, causing excessive stock buildup or critical stockouts.
(Explore how Master Data Management in the Supply Chain prevents such issues here)
Higher Supplier Costs – Without proper vendor master data, companies often purchase materials from multiple suppliers at varying prices, missing out on bulk discounts and optimized sourcing strategies.
Problem | Cost Impact |
---|---|
Duplicate Purchases | Unnecessary purchases of already available stock |
Incorrect Demand Forecasting | Overstocking and stockouts |
Higher Supplier Costs | Inconsistent vendor data delays procurement |
Expedited Shipping Fees | Emergency purchases due to missing or misclassified items |
Case in Point: Material and Vendor Master Creation
A major industrial company faced procurement inefficiencies due to fragmented material and vendor data. Their challenges included:
- Duplicate materials listed under different names.
- Supplier redundancies leading to lost volume discounts.
- Manual intervention needed for order processing.
Solution & Impact:
After implementing a structured material and vendor master, the company:
- Reduced procurement errors by 30%
- Optimized supplier selection, leading to better pricing
- Streamlined purchasing processes, cutting down cycle time
Key takeaway: Standardizing material and vendor master data leads to cost savings and improved procurement efficiency.
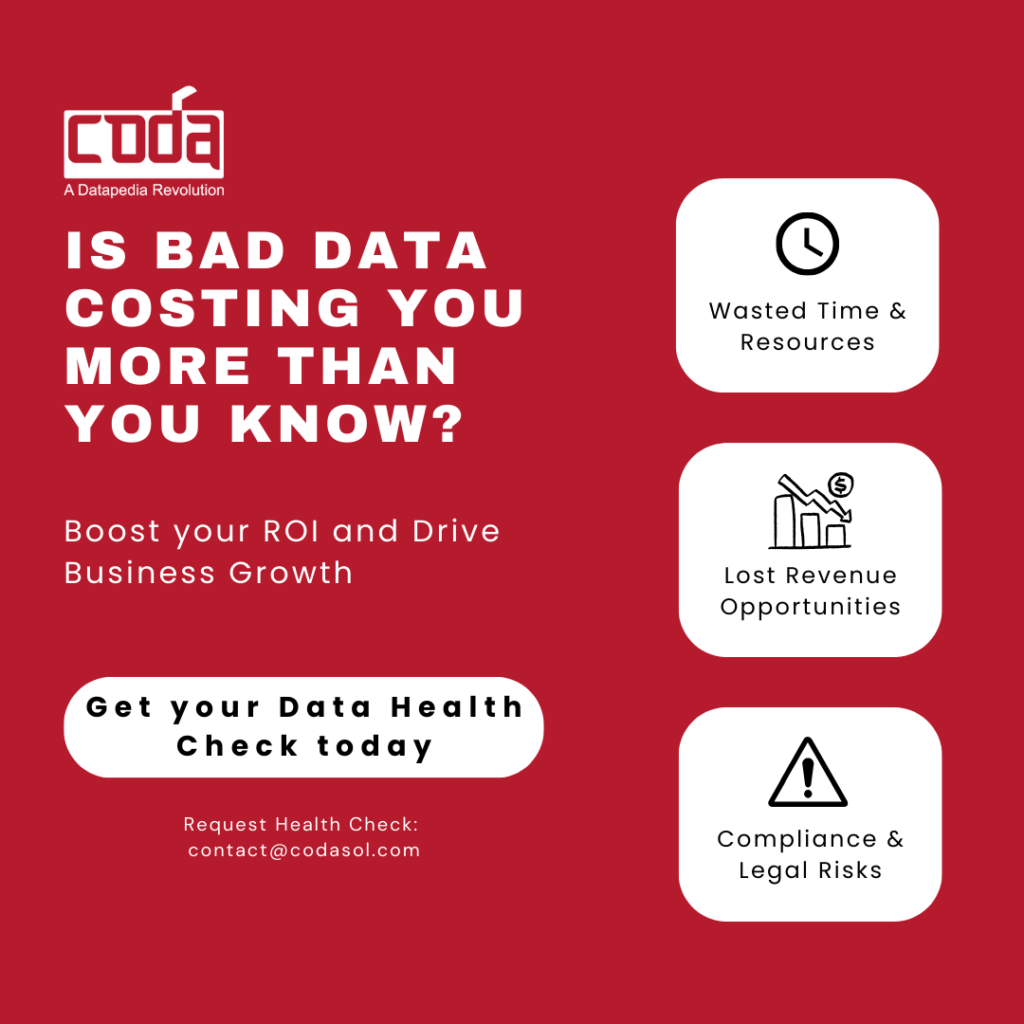
2. Higher Maintenance Costs & Unplanned Downtime
Poor material data can be catastrophic for maintenance teams. When assets and spare parts are not correctly documented, organizations face:
Delayed Repairs – Maintenance teams struggle to identify the correct spare parts due to incorrect naming conventions or missing specifications.
(Learn how MDM Saves Oil & Gas Companies $8.9M in Unplanned Shutdown Costs here)
Unnecessary Spare Parts Purchases – When materials are duplicated or misclassified, companies end up buying spares they already have, leading to inflated MRO inventory costs.
Extended Equipment Downtime – Missing or incorrect parts lead to prolonged equipment failures, affecting overall plant reliability.
(See why Data Cleansing is Essential for Cement Manufacturing here)
Issue | Impact |
---|---|
Missing or Incorrect Parts | Delays in repairs, increasing downtime |
Wrong Spare Parts Installed | Increased equipment failure and maintenance costs |
Inefficient Workflows | Wasted time searching for accurate part information |
Case in Point: Asset Master Data Standardization
A leading energy company experienced frequent maintenance delays due to:
- Missing or outdated asset master data.
- Poorly classified spare parts, leading to excess inventory.
- Difficulty tracking components needed for preventive maintenance.
Solution & Impact:
After standardizing asset master data, they:
- Reduced unplanned downtime by 25%
- Enhanced preventive maintenance scheduling
- Saved millions in maintenance costs
Key takeaway: Accurate material and asset master data are critical for maintenance efficiency and downtime reduction.
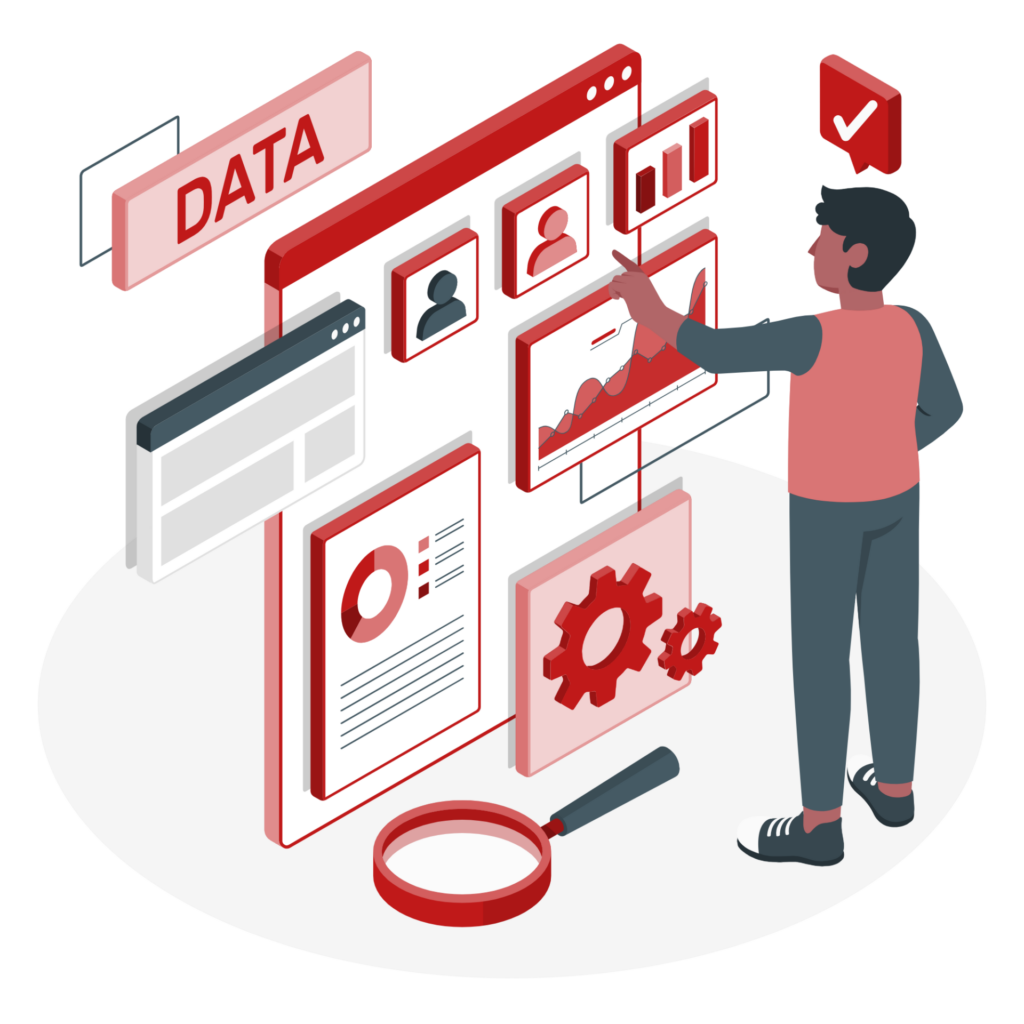
Struggling with data issues? Get a free Material Data Health Check today!
3. Compliance, Safety & Inventory Inefficiencies
Poor material data increases compliance risks, especially in highly regulated industries like Oil & Gas, Chemicals, and Manufacturing.
Audit Failures & Regulatory Fines – Disorganized material master data can lead to inaccuracies in reporting, exposing companies to financial penalties and legal issues.
(See the Importance and Challenges of Data Governance in MDM here)
Supplier & Contract Risks – Inaccurate supplier data makes it difficult to track contract terms, delivery timelines, and quality standards, leading to disputes and supply chain disruptions.
Risk | Consequence |
---|---|
Regulatory Non-Compliance | Fines, legal action, reputational damage |
Safety Hazards | Incorrect parts causing equipment failure and accidents |
Excess Inventory Costs | Overstocking materials due to unreliable data |
Case in Point: Material Data Standardization
A manufacturing company struggled with data inconsistencies across its supply chain, causing:
- Duplicate materials inflating inventory costs.
- Non-compliant materials slipping through procurement.
- Wasted storage space due to poor classification.
Solution & Impact:
By implementing material data standardization, they:
- Cut material costs by 15%
- Eliminated redundant SKUs
- Improved supply chain efficiency
Key takeaway: Standardized material data enhances inventory accuracy and regulatory compliance.
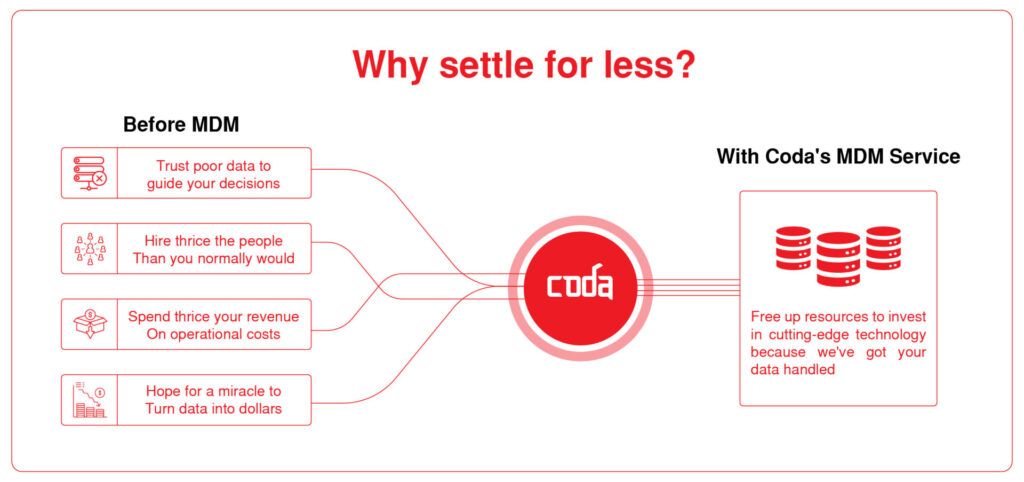
🔗 Related Post: How Master Data Cleansing Enhances Asset Management
How to Fix Poor Material Master Data
1. Implement a Data Cleansing & Standardization Process
- Remove duplicates, obsolete entries, and inconsistencies in material records.
- Standardize naming conventions to improve searchability and reporting.
- Integrate AI-powered de-duplication tools for accuracy.
(Follow the Top 10 Best Practices for Data Cleansing and Standardization in MDM here)
🔗 More Success Stories:
- Data Cleansing & De-duplication – Saving $3.36M
- Material Code Creation – Reducing Procurement Cycle Time
2. Align Material Master Data with ERP & SAP Best Practices
- Ensure material data is structured for seamless ERP integration.
- Use SAP S/4HANA’s data governance framework for consistency.
- Implement BOM and PM Plans in SAP to streamline maintenance planning.
(Discover How AI & Machine Learning Streamline Data Management here)
🔗 More Success Stories:
3. Conduct Regular Data Audits & Governance
- Perform quarterly reviews to maintain data integrity.
- Establish data ownership policies to avoid future inconsistencies.
- Train procurement & maintenance teams on data governance best practices.
(Learn How Cloud MDM Cuts Data Management Costs by 30% here)
Frequently Asked Questions (FAQs)
1. What is material master data?
Material master data is the structured information about materials and spare parts, including descriptions, specifications, suppliers, and pricing.
2. How do poor material master data records lead to duplicate purchases?
Duplicate records arise when materials are stored under different names or descriptions, causing procurement teams to unintentionally order the same item multiple times.
3. Can poor material master data really increase downtime?
Yes! Missing or inaccurate spare part records result in delays in maintenance, leading to costly unplanned downtime.
4. What industries are most affected by poor material master data?
- Manufacturing
- Oil & Gas
- Utilities
- Steel & Cement
- Pharmaceuticals
5. How can I start improving my material master data today?
Start by auditing your current data, identifying duplicates, and using AI-driven solutions to clean and standardize records.
Conclusion: Turn Data into a Cost-Saving Asset
Poor material master data is a profitability problem. With the right data management strategy, you can:
- Reduce procurement costs by eliminating duplicate purchases
- Optimize maintenance operations and minimize downtime
- Improve inventory accuracy for better forecasting
🔗 Related Post: How Master Data Standardization Improves Supply Chain Efficiency
Invest in Clean Data for Maximum ROI
Would you like a free consultation on how to optimize your material data?
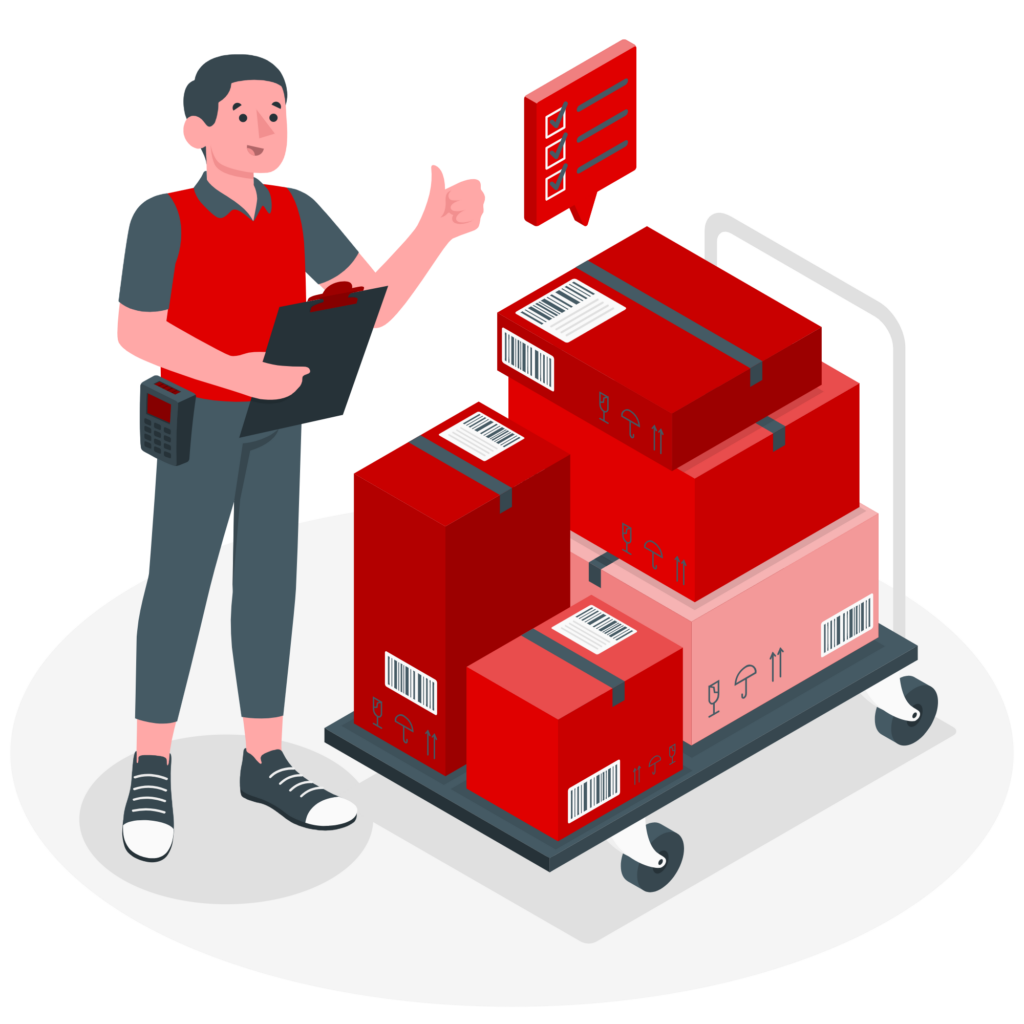