Unplanned downtime can be a significant financial drain on businesses, leading to lost production, increased maintenance costs, and decreased operational efficiency. Enterprise Asset Management (EAM) reduces unplanned downtime by implementing proactive maintenance strategies, optimizing asset performance, and ensuring seamless workflow integration.
In this blog, we’ll explore how EAM prevents unexpected failures, the role of predictive maintenance, real-world case studies, and best practices for implementing EAM effectively.
What is Enterprise Asset Management (EAM)?
Enterprise Asset Management (EAM) is a systematic approach to managing an organization’s physical assets throughout their lifecycle. It involves tracking, maintaining, and optimizing assets using digital tools like Computerized Maintenance Management Systems (CMMS), IoT, and AI-driven predictive analytics.
Key Features of EAM
Feature | Description |
---|---|
Predictive Maintenance | Uses IoT sensors and AI to predict asset failures before they happen |
Work Order Management | Automates scheduling and tracking of maintenance tasks |
Asset Lifecycle Management | Tracks assets from procurement to disposal |
Inventory Optimization | Ensures spare parts availability, reducing repair delays |
Compliance & Safety | Meets regulatory standards for asset maintenance |
Read more the power of preventive maintenance in cement industry
How EAM Reduces Unplanned Downtime
EAM provides a structured approach to asset lifecycle management, leveraging predictive maintenance, real-time monitoring, and standardized processes. Key ways EAM minimizes downtime include:
1. Predictive Maintenance (PdM)
EAM integrates IoT sensors and AI-driven analytics to predict failures before they occur. By analyzing real-time data, organizations can shift from reactive to predictive maintenance, reducing unplanned downtime.
2. Preventive Maintenance (PM)
EAM automates scheduled maintenance based on usage patterns, ensuring timely servicing and reducing breakdowns. A well-structured PM plan prevents minor issues from escalating into costly failures.
3. Asset Data Standardization
Inconsistent asset data leads to inefficiencies in maintenance planning. EAM ensures standardized asset master data, enabling accurate tracking, maintenance scheduling, and spare parts management.
4. Work Order Management
An EAM system automates work order processes, ensuring swift issue resolution. It enables technicians to access asset history, diagnose problems efficiently, and implement corrective actions.
5. Spare Parts & Inventory Optimization
Unavailability of critical spare parts prolongs downtime. EAM systems track spare parts usage and optimize inventory levels to ensure parts availability when needed.
Benefits of EAM in Reducing Downtime
Benefit | Impact |
Proactive Maintenance | Detect issues early and prevent failures. |
Data-Driven Decision-Making | Leverage real-time analytics for asset management. |
Optimized Spare Parts Management | Ensure availability of critical components. |
Regulatory Compliance | Meet industry safety and compliance standards. |
Improved Operational Efficiency | Reduce maintenance time and increase productivity. |
Case Studies:
Case Study 1: Asset Management for a Leading Energy & Utility Company
Challenge
A leading energy and utility company struggled with frequent unplanned outages due to poor asset visibility and inconsistent maintenance schedules.
Solution
CODASOL implemented an Enterprise Asset Management system that standardized asset data, automated preventive maintenance, and integrated real-time monitoring.
Results
- 30% reduction in unplanned downtime
- Improved asset tracking & performance monitoring
- Enhanced regulatory compliance
Case Study 2: BOM & PM Plan Creation in SAP for a Chemical Industry
Challenge
A chemical manufacturing company faced unexpected shutdowns due to lack of preventive maintenance planning and inconsistent Bill of Materials (BOM) for assets.
Solution
CODASOL implemented BOM creation and PM plan integration in SAP, enabling structured maintenance scheduling and accurate spare parts tracking.
Results
- 25% improvement in maintenance efficiency
- Significant reduction in unexpected failures
- Optimized spare parts inventory
Best Practices for Implementing EAM Effectively
1. Integrate EAM with IoT and AI
Leverage IoT sensors and AI-driven analytics for real-time monitoring and predictive insights.
2. Standardize Maintenance Workflows
Establish standard operating procedures (SOPs) for preventive maintenance, inspections, and emergency repairs.
3. Train Employees on EAM Systems
Ensure maintenance teams and operators are well-versed in using EAM tools for data-driven decision-making.
4. Regularly Audit and Optimize EAM Processes
Conduct periodic performance audits to refine asset management strategies and improve ROI.
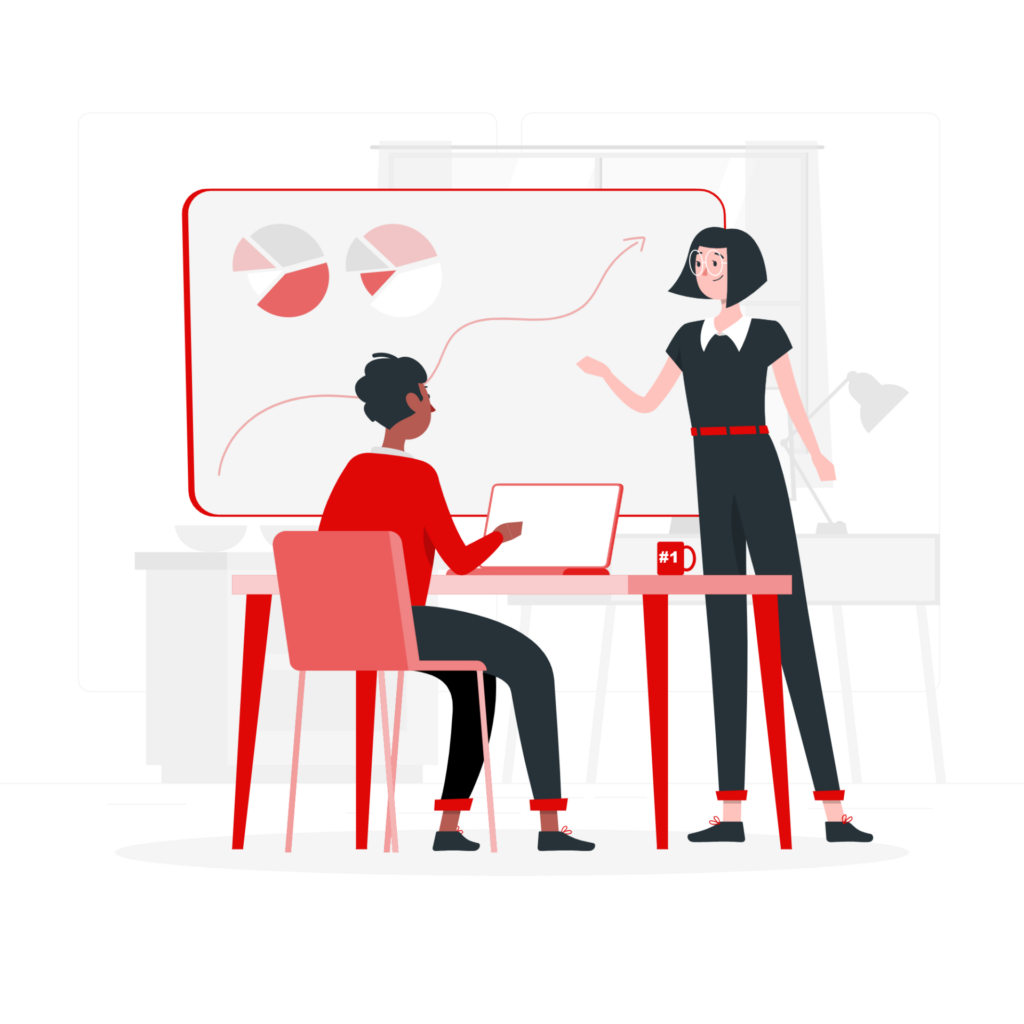
Optimize Your Asset Performance Today! Contact our EAM experts for a free consultation.
FAQs
1. How does EAM differ from CMMS?
EAM is a comprehensive asset management system covering the entire asset lifecycle, while CMMS focuses on maintenance management.
2. What industries benefit the most from EAM?
Industries such as manufacturing, oil & gas, utilities, healthcare, and logistics benefit from reduced downtime and optimized asset utilization.
3. Can EAM integrate with existing ERP systems?
Yes, modern EAM solutions integrate with ERP, SCM, and financial systems to ensure seamless data flow and decision-making.
4. What’s the ROI of implementing EAM?
Companies experience an ROI of 3x-5x within the first 12-24 months, depending on implementation scale and industry.
5. What are the key KPIs to measure EAM effectiveness?
Key KPIs include Mean Time Between Failures (MTBF), Mean Time to Repair (MTTR), Asset Utilization Rate, and Maintenance Cost Reduction.
Conclusion
Enterprise Asset Management (EAM) reduces unplanned downtime by enabling predictive maintenance, optimizing asset reliability, and ensuring efficient resource allocation. Companies adopting EAM experience significant cost savings, improved productivity, and extended asset lifespan.
Investing in a robust EAM strategy is crucial for businesses aiming to minimize downtime, increase efficiency, and enhance profitability.
Ready to transform your asset management strategy? Contact us today to explore how EAM can revolutionize your business operations: contact@codasol.com