The petrochemical industry in India, GCC, and the Far East faces growing challenges in asset tracking, predictive maintenance, and regulatory compliance. With increasing operational complexities and rising maintenance costs, 3D digital twins in asset tracking are emerging as a game-changer.
Leading markets such as Saudi Arabia, UAE, China, and India are investing heavily in smart asset management solutions to reduce downtime, enhance efficiency, and improve safety standards.
By integrating IoT sensors, AI, and machine learning (ML), businesses can digitally replicate their physical assets, enabling better decision-making and significant cost savings.
What Is a 3D Digital Twin?
A 3D digital twin is a virtual representation of a physical asset that updates in real time using sensor data, AI, and cloud computing. It allows petrochemical companies to track, analyze, and predict asset performance, ensuring seamless operations.
How It Works
- Data Collection: IoT sensors capture real-time data from assets.
- Digital Modeling: AI and 3D visualization create an exact replica.
- Continuous Monitoring: Predictive analytics detect potential failures before they happen.
- Optimization: Simulations test various operational scenarios for efficiency improvements.
Why the Petrochemical Industry Needs 3D Digital Twins
1. Real-Time Asset Tracking
- Eliminates manual tracking with automated data collection
- Improves visibility into remote or hazardous environments
- Reduces errors and discrepancies in asset records
2. Predictive Maintenance & Downtime Reduction
- AI-driven insights detect early signs of equipment failure
- Reduces unexpected shutdowns by 30-40%
- Extends the lifespan of critical assets
3. Enhanced Operational Efficiency
- Identifies bottlenecks and inefficiencies
- Simulates different workflows to optimize processes
- Lowers energy consumption and waste
4. Improved Safety & Risk Management
- Enables virtual training for high-risk maintenance tasks
- Simulates emergency scenarios to improve response times
- Reduces exposure to hazardous conditions
5. Cost Savings & Compliance
- Avoids costly downtime and emergency repairs
- Helps meet regulatory and safety compliance standards
- Reduces insurance costs by lowering operational risks
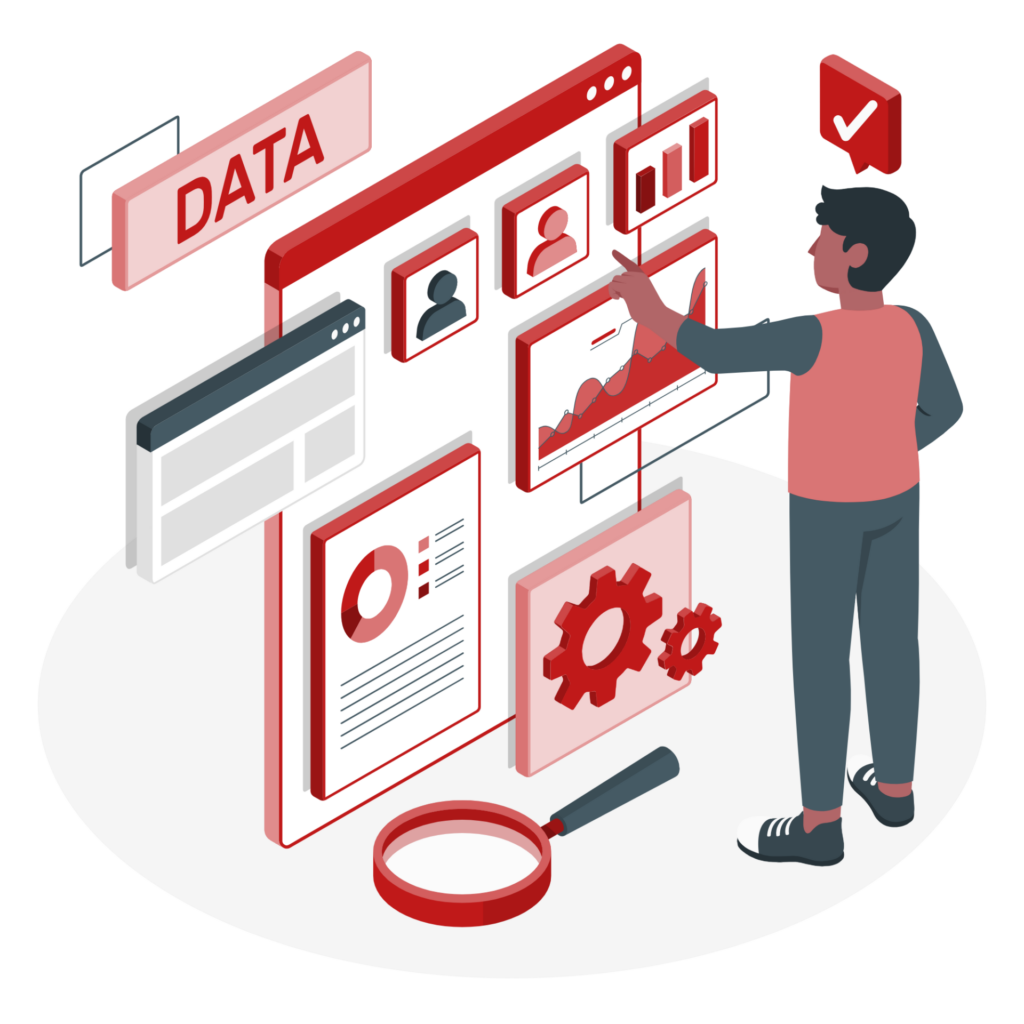
Want to enhance asset tracking and reduce downtime?
Real-World Applications of 3D Digital Twins in Asset Tracking
Application | Impact |
---|---|
Equipment Health Monitoring | Tracks real-time asset conditions and predicts failures. |
Remote Inspections | Reduces the need for manual checks in hazardous areas. |
Operational Simulation | Tests new workflows before implementation. |
Supply Chain Optimization | Enhances material flow and inventory management. |
Regulatory Compliance | Ensures adherence to safety and environmental regulations. |
Case Study: How a Leading Petrochemical Plant Improved Efficiency
A GCC-based petrochemical company adopted 3D digital twins for asset tracking and experienced:
- 22% reduction in maintenance costs through predictive insights
- 30% fewer unplanned shutdowns with real-time monitoring
- Improved regulatory compliance with automated reporting
- 15% increase in operational efficiency by optimizing workflows
Also read:
3D Digital Twins vs. Traditional Asset Tracking
Feature | Traditional Asset Tracking | 3D Digital Twins |
---|---|---|
Data Collection | Manual, periodic | Automated, real-time |
Accuracy | Prone to human error | Highly accurate |
Maintenance Approach | Reactive (after failure) | Predictive (before failure) |
Operational Insights | Limited analysis | AI-powered analytics |
Safety & Risk Management | Reactive measures | Proactive risk prevention |
Frequently Asked Questions (FAQs)
1. How does a 3D digital twin differ from traditional asset tracking?
Traditional asset tracking relies on manual data collection, whereas digital twins use real-time IoT data to create a live, interactive replica of assets, enabling predictive analytics and automation.
2. What industries can benefit from 3D digital twins?
Apart from petrochemicals, digital twins are widely used in oil and gas, manufacturing, utilities, construction, marine, defense, aviation, and healthcare.
3. Is it expensive to implement 3D digital twins?
While the initial investment may be higher, the long-term savings in maintenance, downtime, and operational efficiency far outweigh the costs.
4. Can 3D digital twins integrate with existing ERP systems?
Yes, they can seamlessly integrate with SAP, Oracle, Maximo, and other ERP platforms for better data management and decision-making.
5. How secure is the data in a digital twin?
With cloud-based encryption, AI-driven security measures, and access controls, digital twins provide high-level cybersecurity protection.
Final Thoughts
The adoption of 3D digital twins is reshaping asset tracking, predictive maintenance, and operational efficiency in the petrochemical industry. Companies that embrace this digital transformation will experience:
- Faster maintenance cycles
- Lower operational costs
- Higher equipment uptime
- Better risk management
Ready to revolutionize your asset tracking? Contact us today for a free consultation.
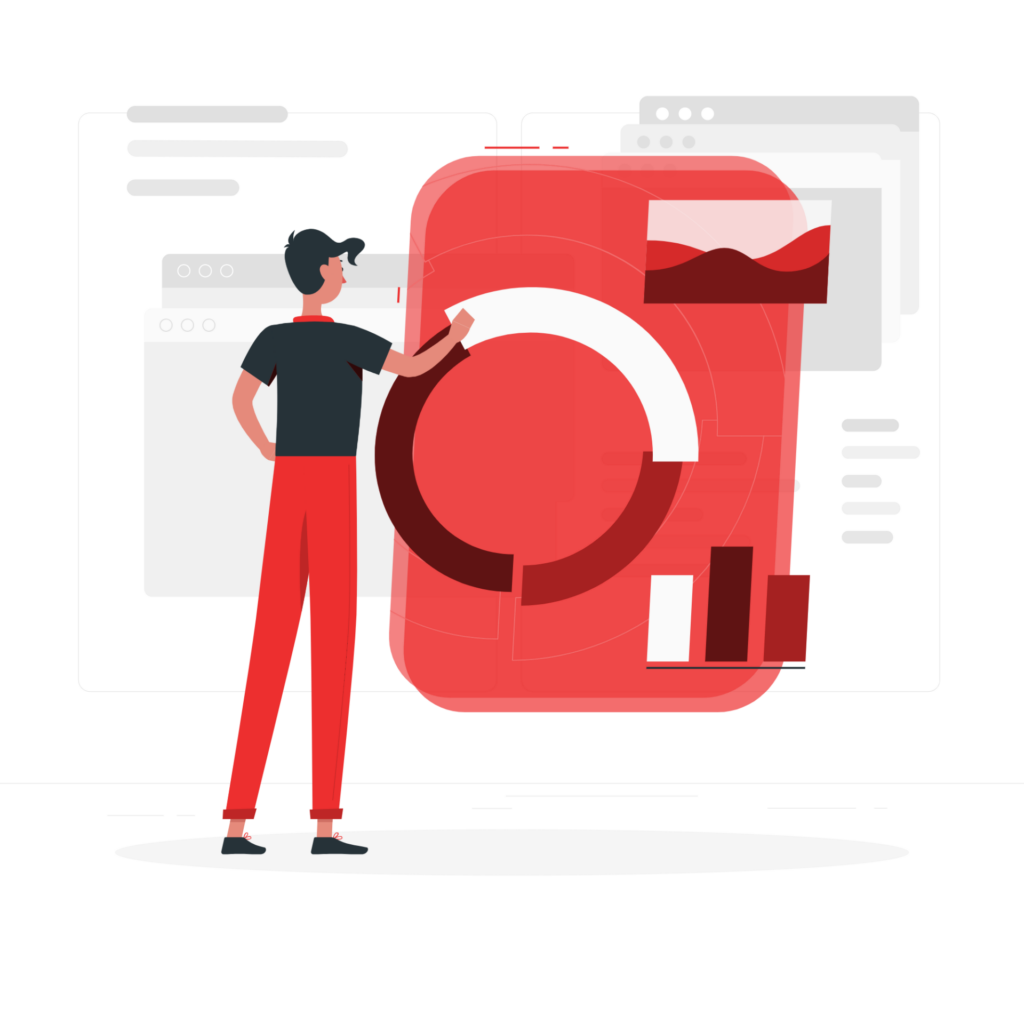