In capital-intensive industries, inventory often represents a substantial portion of operational costs. From Oil & Gas rigs in the Gulf to manufacturing plants in India and healthcare institutions across the Far East, inefficient inventory management can drain resources, delay operations, and create significant financial risk.
But what if there was a smarter way to manage it all?
This blog explores inventory optimization strategies tailored for capital-intensive industries operating in India, the GCC, and the Far East.
Why Inventory Optimization Matters in Capital-Intensive Industries
Capital-intensive sectors such as Oil & Gas, Utilities, Real Estate & Construction, Marine & Ports, Healthcare, EPC, and Aviation depend heavily on uninterrupted operations. Any disruption due to stockouts, overstocking, or inaccurate data can lead to downtime, compliance issues, or delayed service delivery.
Key challenges include:
- Excessive capital locked in non-moving or obsolete inventory
- Duplicate materials in the master database
- Lack of visibility across multi-location warehouses
- Manual processes with low data accuracy
- Inability to forecast demand accurately
The right inventory optimization strategy transforms these challenges into savings, agility, and business resilience.
Top 7 Inventory Optimization Strategies for Capital-Intensive Industries
1. Master Data Management (MDM) for Material Masters
A clean, standardized, and deduplicated material master lays the foundation for inventory optimization. By eliminating duplicates and categorizing materials accurately, organizations can:
- Avoid over-purchasing
- Reduce operational delays
- Standardize procurement
Example: A utility company in the UAE reduced its inventory by 18% after implementing an MDM solution.
2. ABC-VED Analysis
Combining ABC (value-based) and VED (criticality-based) classification helps prioritize items that are both high-cost and mission-critical.
- Category A-V: High-value, very essential → strict control
- Category C-E: Low-value, essential → monitored regularly
- Category B-D: Moderate value, desirable → controlled cyclically
This hybrid analysis supports smarter stocking decisions and better resource allocation.
3. Predictive Demand Forecasting
Using AI/ML algorithms, companies can forecast demand for spares and consumables based on:
- Equipment usage patterns
- Historical consumption
- Seasonality and project timelines
Result: Fewer stockouts, optimized procurement cycles, and reduced emergency orders.
4. Inventory Visibility Across Sites
Integrating ERP and WMS systems enables a single view of stock across warehouses. Especially beneficial for:
- EPC firms with multiple project sites
- Marine ports with decentralized storage
- Government or defense institutions with varied stock points
This allows inter-warehouse transfers and smarter procurement planning.
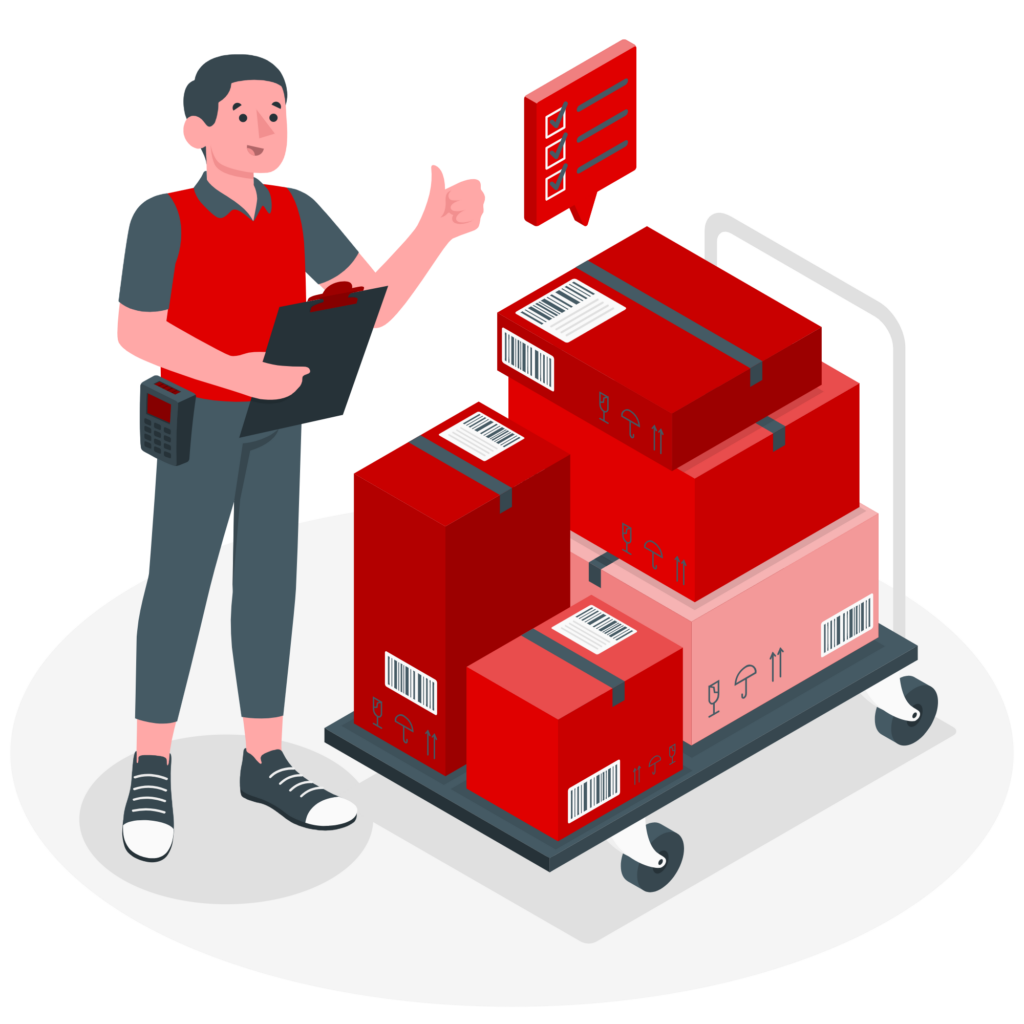
Want to reduce your inventory holding cost by 20% in the next 6 months?
5. Consignment & Vendor Managed Inventory (VMI)
By collaborating with suppliers, businesses can shift inventory ownership until consumption. VMI benefits include:
- Reduced working capital
- Better supplier alignment
- Improved fill rates
Particularly useful in the EPC, and Construction sectors where project timelines fluctuate.
6. Lifecycle-based Spare Parts Planning
Every asset has a lifecycle, and so does the need for its spare parts. By aligning inventory with the asset’s maintenance phase:
- Reduce overstock in early phases
- Prepare for peak replacement periods
- Avoid obsolete stock during asset decommissioning
7. Data-Driven Procurement Strategy
With real-time data insights:
- Track fast-moving and non-moving stock
- Optimize reorder points
- Eliminate “just in case” stocking mentality
Bonus Tip: Use dashboards for real-time alerts and KPI tracking.
Inventory Optimization at a Glance
Strategy | Impact | Best For |
---|---|---|
MDM & Deduplication | 10–20% Inventory Reduction | Oil & Gas, EPC, Utilities |
ABC-VED Analysis | Risk-Based Stock Control | Healthcare, Aviation, Manufacturing |
Predictive Forecasting | Demand Accuracy ↑, Stockouts ↓ | Marine, Construction, Minerals & Metals |
Cross-Site Visibility | Reduced Emergency Procurement | Government, Defense, Ports |
VMI / Consignment | Cash Flow Improvement | EPC, Real Estate, Healthcare |
Lifecycle Spare Planning | Obsolescence Avoidance | Engineering, Manufacturing, Aviation |
Data-Driven Procurement | Cost & Process Efficiency | Banking, Utilities, Construction |
Inventory Optimization Strategies Checklist
Here’s a practical checklist to audit your inventory management maturity:
Data Foundation
- Material Master data deduplicated and standardized
- BOM (Bill of Materials) correctly linked to assets
- Vendor and item catalog rationalized
Classification & Analysis
- ABC-VED analysis implemented
- FSN (Fast-Slow-Nonmoving) analysis completed
- XYZ analysis for demand variability done
Inventory Control Policies
- Reorder levels and EOQ (Economic Order Quantity) defined
- Safety stock parameters reviewed quarterly
- Minimum-Maximum stock levels automated
Process Optimization
- Regular stock audits scheduled
- Aging inventory reports reviewed monthly
- Inter-warehouse transfers enabled via system
Technology & Automation
- Integrated with ERP (SAP/Oracle/Maximo)
- AI/ML-based demand planning tool in place
- Real-time dashboards for inventory KPIs
Collaborative Supply Chain
- Vendor Managed Inventory (VMI) options explored
- Supplier performance metrics tracked
- Contract terms linked to consumption-based models
Sustainability & Circularity
- Surplus and obsolete inventory identified for resale
- Idle asset exchange or liquidation strategy in place
- Inventory digitalization aligned with ESG goals
Regional Considerations:
- India: Focus on digital transformation, central procurement & public-private collaboration
- GCC (UAE, Saudi, Oman): High reliance on imported spares, ERP adoption rising
- Far East (Singapore, Malaysia, Japan): Strong automation, supply chain digitization, AI integration
Customizing inventory strategies based on local challenges and supply chain maturity is essential for success.
Bonus: Inventory Optimization Topics for Deeper Exploration
If you want to go deeper in your optimization journey, here are some advanced themes to explore:
1. Inventory Optimization KPIs to Track
- Inventory Turnover Ratio
- Days Inventory Outstanding (DIO)
- Service Level %
- Inventory Accuracy
- Stockout Rate
2. Role of AI/ML in Inventory Optimization
- Real-time anomaly detection
- Predictive demand algorithms
- Automated safety stock management
3. Inventory Optimization During Supply Chain Disruptions
- Port delays, pandemics, geopolitical instability
- Resilience planning via digital twins and scenario modeling
4. Linking Inventory to ESG Goals
- Reducing expired/obsolete stock
- Greener logistics
- Sustainable sourcing tied to inventory policy
FAQs: Inventory Optimization for Capital-Intensive Industries
1. What is inventory optimization in capital-intensive sectors?
It’s the process of balancing inventory levels to meet demand while minimizing costs, risks, and waste in asset-heavy industries like Oil & Gas, EPC, or Healthcare.
2. How can data help optimize inventory?
Accurate, deduplicated data helps avoid overstocking, improves procurement accuracy, and enables automation of stock control processes.
3. Is inventory optimization a one-time project?
No. It’s a continuous improvement journey starting with data cleanup, followed by analysis, technology adoption, and performance monitoring.
4. What tools are used for inventory optimization?
ERP systems (SAP, Oracle), MDM platforms, AI-based forecasting tools, and dashboard-based reporting tools are commonly used.
5. What’s the ROI of inventory optimization?
Companies typically see ROI within 6–12 months through reduced inventory costs, better cash flow, and increased asset uptime.
Start building a lean, intelligent, and future-ready inventory ecosystem. One strategy at a time.
If you need help creating your customized roadmap, we’re just an e-mail away: contact@codasol.com
Get a tailored inventory optimization roadmap for your industry & region.
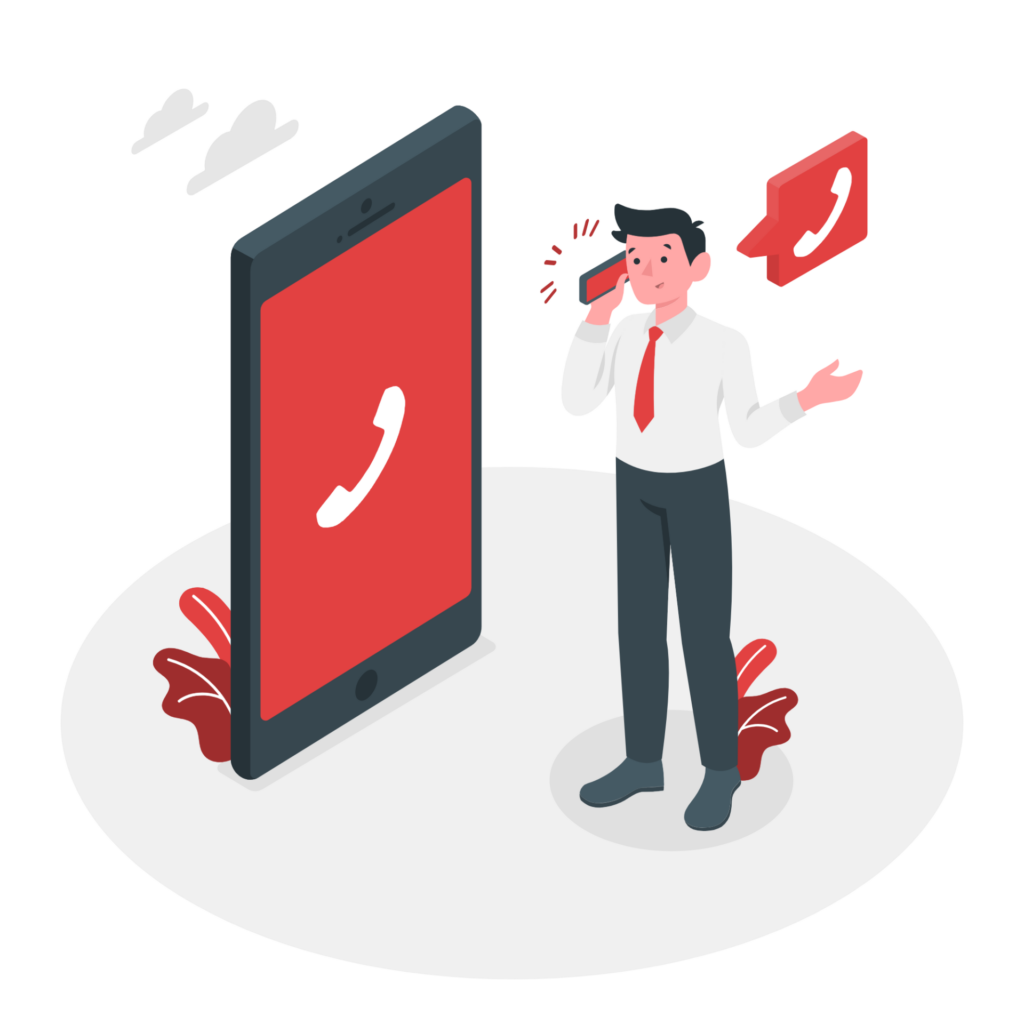