The manufacturing industry is undergoing a transformative shift thanks to AI and GenAI in manufacturing. As technology evolves, these intelligent systems bring new opportunities for optimization, efficiency, and innovation. By incorporating AI and generative AI (GenAI) into the manufacturing process, companies can create smarter workflows, increase profitability, and deliver products faster and with greater precision.
In this blog, we will explore how AI and GenAI are changing the landscape of the manufacturing sector, their applications, the significant benefits, and the challenges businesses must consider before implementing these technologies.
What is AI in Manufacturing?
Artificial Intelligence (AI) refers to machines or software that simulate human intelligence to perform tasks. It includes technologies like machine learning, natural language processing (NLP), and deep learning. In manufacturing, AI is used to optimize processes, enhance decision-making, and boost productivity.
By automating mundane tasks and improving the accuracy of operations, AI enables manufacturers to streamline production, improve product quality, and reduce costs.
AI is the backbone of modern manufacturing because it helps businesses shift from traditional, manual methods to smarter, more efficient processes. From predictive maintenance to inventory management, AI enables manufacturers to anticipate challenges, improve resource allocation, and stay competitive in a rapidly changing market.
What is GenAI?
Generative AI (GenAI) is a subset of AI that uses algorithms to create new content or solutions rather than simply analyzing data or performing predefined tasks. Unlike traditional AI, which is based on analyzing historical data to predict outcomes, GenAI generates novel outputs, including product designs, images, videos, and even entire processes.
In manufacturing, GenAI empowers businesses to innovate rapidly, automate design processes, and optimize workflows. This transformative technology is helping companies reduce waste, improve sustainability, and increase operational efficiency by predicting and addressing potential problems before they occur.
Use Cases of AI and GenAI in Manufacturing
Predictive Maintenance
Predictive maintenance is one of the most prominent use cases of AI in manufacturing. By using AI algorithms and sensors, companies can monitor equipment in real-time, predict potential breakdowns, and schedule maintenance before failures occur. Predictive maintenance minimizes downtime, reduces repair costs, and extends the lifespan of machines, ultimately leading to a more efficient production process.
For example, AI can monitor machinery vibrations, temperature fluctuations, and other sensor data to identify potential issues before they lead to unplanned shutdowns. This enables businesses to optimize maintenance schedules and avoid costly repairs or replacements.
Digital Twin Technology
A digital twin is a virtual model that represents a physical asset, process, or system. Using data from IoT sensors and AI, manufacturers can create real-time digital replicas of machines, production lines, or even entire factories. These digital twins provide valuable insights into the performance of physical assets, enabling manufacturers to simulate different scenarios and optimize processes without interrupting operations.
For instance, digital twins allow companies to predict equipment failures, optimize layouts, and test new production methods. They also facilitate remote monitoring, enabling manufacturers to make data-driven decisions and prevent costly errors.
Mass Customization
Mass customization refers to the ability to produce tailored products at scale. AI plays a crucial role in enabling manufacturers to adapt their production lines to meet individual customer preferences while maintaining efficiency and cost-effectiveness. Through AI-powered systems, businesses can analyze customer feedback, purchasing behavior, and market trends to create customized products in real-time.
For example, AI can be used to adapt manufacturing processes based on customer orders, allowing manufacturers to deliver unique products without the need for costly retooling or additional labor. This results in higher customer satisfaction and a more flexible manufacturing system.
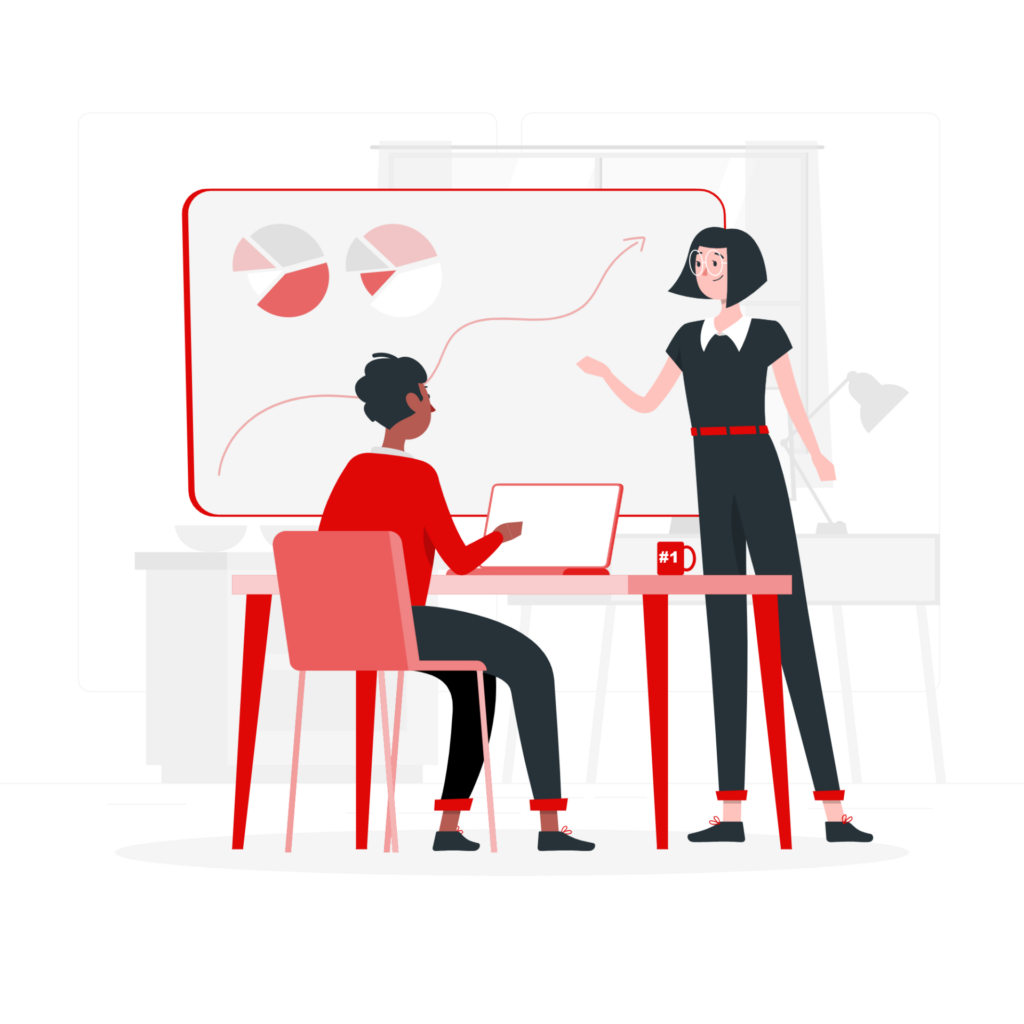
Partner with Codasol today to explore tailored solutions that enhance efficiency, reduce costs, and drive innovation in your production line.
Collaborative Robots (Cobots)
Collaborative robots or cobots are designed to work alongside human operators in a manufacturing environment. Unlike traditional robots that are isolated in cages or specific zones, cobots are programmed to assist workers in tasks such as assembly, packaging, and inspection. These robots are particularly useful in repetitive or physically demanding jobs, where they can reduce strain on human workers and improve production speed and accuracy.
Cobots have the added benefit of being more easily integrated into existing workflows. They can work collaboratively with humans, increasing safety, reducing error rates, and optimizing production efficiency.
Inventory Management
AI can enhance inventory management by predicting demand more accurately and optimizing stock levels. AI algorithms analyze historical sales data, market trends, and customer behavior to forecast future demand. This enables manufacturers to avoid stockouts or overstocking, leading to cost savings and more efficient operations.
Also, AI can automate the ordering process, ensuring that the right materials are available at the right time, reducing lead times, and improving supply chain efficiency.
Assembly Line Optimization
AI can optimize assembly lines by analyzing performance metrics and adjusting workflows in real-time. Through predictive maintenance and machine learning algorithms, AI identifies inefficiencies and suggests adjustments that improve the overall productivity of the assembly line. These adjustments can range from optimizing machine speed to reconfiguring workflows to maximize output and minimize downtime.
By leveraging real-time data from sensors and AI systems, manufacturers can ensure that their assembly lines operate at peak efficiency, reducing production costs and ensuring high-quality output.
Benefits of AI and GenAI in Manufacturing
Improved Decision-Making
AI and GenAI help manufacturers make better, data-driven decisions. With real-time insights into production performance, predictive maintenance schedules, and customer demands, businesses can make proactive decisions that enhance operations and reduce risks.
Cost Optimization
AI and GenAI reduce costs by automating repetitive tasks, improving resource allocation, and minimizing errors. Predictive maintenance and inventory optimization further cut costs by reducing the need for repairs, overstocking, and stockouts.
Enhanced Product Quality
AI-driven computer vision and quality control systems can detect defects faster and more accurately than humans. This leads to higher product quality, fewer defects, and more satisfied customers.
Increased Efficiency
AI-powered cobots and automated systems streamline production, reduce human error, and improve speed. This results in greater efficiency, continuous production, and lower labor costs.
Sustainability
AI and GenAI contribute to sustainability by reducing waste, optimizing energy consumption, and improving the recyclability of materials. Also, AI systems enable manufacturers to design environmentally friendly products by analyzing the full lifecycle of products.
Competitive Advantage
Adopting AI and GenAI technologies gives manufacturers a competitive edge by increasing productivity, enhancing innovation, and enabling them to respond quickly to market changes.
Challenges of Adopting AI and GenAI in Manufacturing
While AI and GenAI offer significant benefits, there are challenges that manufacturers must consider:
High Initial Investments
The adoption of AI and GenAI technologies requires substantial investment in hardware, software, and infrastructure. Manufacturers need to budget for not only the purchase of advanced systems but also for the training and development of employees to use these technologies effectively.
Data Quality
AI systems rely heavily on high-quality, consistent, and accurate data. If the data fed into the systems is outdated or incomplete, the entire AI-driven process can break down, leading to inefficiencies and incorrect predictions.
Data Security and Privacy
The use of AI and GenAI often involves analyzing vast amounts of sensitive data. Manufacturers must ensure that their data is secure and that they comply with privacy regulations. Data breaches or non-compliance with regulations can lead to significant financial and reputational damage.
Integration with Legacy Systems
Many manufacturing businesses still rely on outdated legacy systems, which may not be compatible with new AI technologies. The integration of AI into existing systems can be complex and time-consuming, requiring significant changes to workflows.
Skills Gap
AI and GenAI require highly specialized skills to implement and manage. The shortage of skilled professionals in AI and machine learning can hinder the successful adoption of these technologies.
Wrapping Up: Embracing the Future of Manufacturing with AI and GenAI
AI and GenAI are revolutionizing the manufacturing industry by enabling smarter production, improving efficiency, and driving innovation. While the technology offers immense potential, manufacturers must carefully consider the challenges, including investment costs, data quality, and the integration of new systems. However, with the right strategy, businesses can leverage AI and GenAI to gain a competitive edge, enhance customer satisfaction, and optimize their operations for long-term success.
Are you prepared to integrate AI and GenAI into your operations and get started on a customized, data-driven journey that optimizes your manufacturing processes and boosts your bottom line?
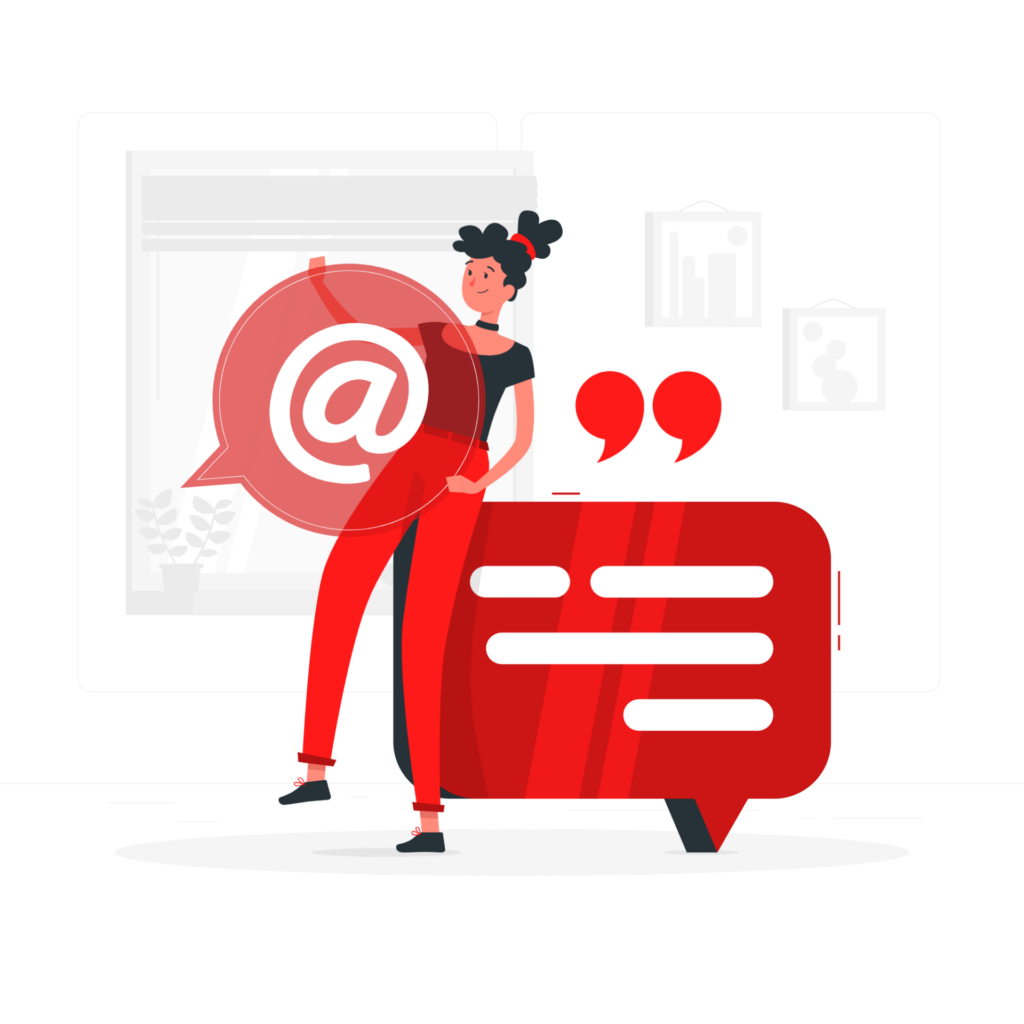