About the client
Our client is a global leader in the chemical industry, dedicated to sustainability and advancing a circular, low-carbon economy. As a top producer of polymers and a pioneer in polyolefin technologies, they create high-quality products that enhance transportation, food safety, clean water, and healthcare. Their commitment to innovation and sustainability plays a crucial role in building a better world.
Challenges
- Collecting documents from the client server for the PCE Project, as most of them are scanned copies of old documents.
- Collecting data for mandatory values when not available in the data sheet; this will be collected from manufacturer websites or catalogs.
- Identifying the reference PM plan from SAP for similar equipment as the existing PM.
- Long texts are either incomplete or not formatted properly, so many PM plans need to be reviewed thoroughly.
Project Scope
A. Asset master data Deletion, creation and
Updation in SAP for Plant Upgradation
Projects including BOM Creation and PM
Plan creation in SAP by analysing existing
data maintained in SAP for the respective
Plant
B. Gaps Assessment and Closure for the
Production Critical Equipments by verify
Existing SAP data of Eqpt, BOM and PM.
Identify missing/wrong information of the
PCE list with reference guidelines and
Update correct and complete data
Work Strategy
A. Plant Upgradation Projects
- Access the site folder through the Citrix workspace and review documents available in the shared folder of the specific project.
- Collect tags from the marked areas of Demo and Revised P&ID and populate them in the equipment template for deletion, update, and creation after verifying in SAP.
- Create FLOCs in SAP, assign class, and populate make, model, and characteristic values.
- Upload data in the SAP-MDG tool after getting approval for the template from the site and complete equipment updates.
- Create a material template with complete instruments and motors as spares, including recommended spares for machinery.
- Identify unique spares and verify duplicate materials in SAP. Update noun/modifier, quote prices for stock items, and characteristic values of new spares.
- Upload data in the SAP-MDG tool after getting approval for the template and site input for stock and non-stock items, then BOM-link the material codes with the respective equipment.
- Create a PM template to update existing PMs or create a new PM, and populate data from related equipment in SAP.
- Create a task list and new PM in SAP after getting approval for the template from the site.
B. PCE Gap Assessment and Gap Closure Projects Projects
Gap Assessment: Verify PCE list equipment data in SAP and identify tags not created in SAP, incorrect class assignments, and missing criticality classes. Check BOM linked with equipment and identify missing BOMs. Ensure that a PM plan exists in SAP for all PCE tags and verify the tasks with the Equipment Maintenance Strategy (EMS) to identify gaps.
Gap Closure: Create equipment and material templates for the required updates. Review site comments for the gaps in PM and create PM templates accordingly. Equipment creation, basic class updates, and production criticality updates are uploaded in the SAP-MDG tool to complete equipment updates. New material codes are also created, and BOMs are linked with the respective equipment. New PM plans and updates to long text as per EMS are completed in SAP.
Work Flow – BOM Creation and PM Plan creation in SAP
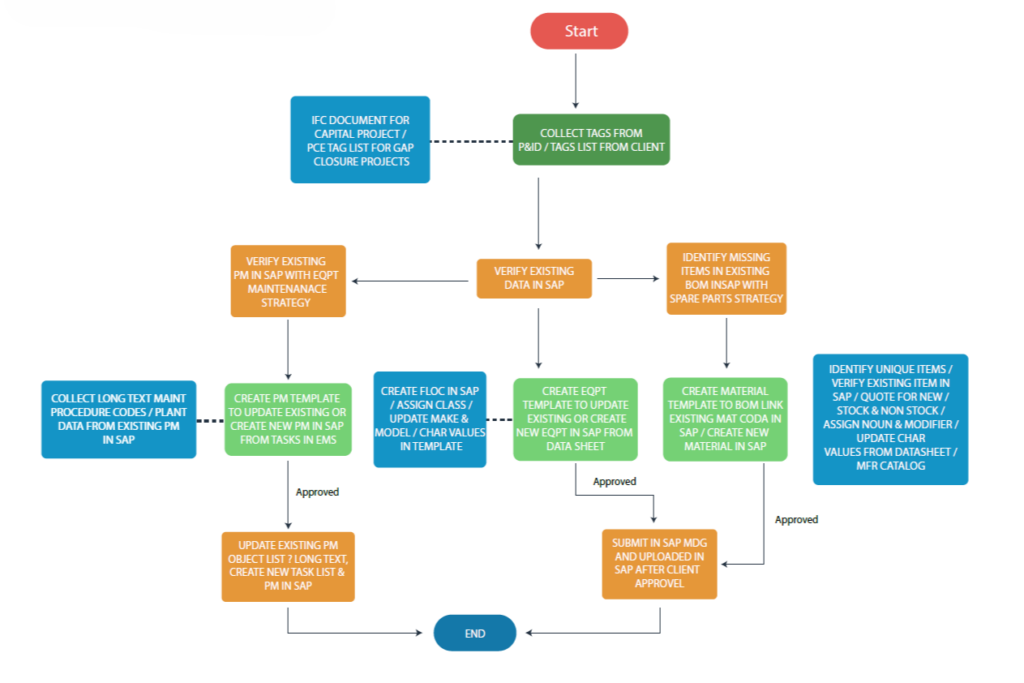