Efficient inventory management is a critical challenge for fertilizer and chemical plants. Excess inventory leads to high carrying costs, while stockouts disrupt operations. By implementing data-driven inventory standardization, plants can eliminate duplicate materials, streamline procurement, and enhance decision-making, leading to inventory cost reduction.
Data standardization is a proven strategy to optimize inventory, reduce costs, and improve supply chain efficiency. In this guide, we explore how fertilizer and chemical manufacturers can leverage data standardization to achieve significant cost savings.
The Impact of Poor Inventory Management in Fertilizer & Chemical Plants
Without proper data standardization, fertilizer and chemical plants face:
- Duplicate inventory, increasing storage and procurement costs
- Inconsistent material descriptions, leading to misidentification and delays
- Excess safety stock, tying up working capital
- Procurement inefficiencies, causing price variances and supplier redundancies
Implementing data standardization ensures inventory data is accurate, consistent, and structured, enabling inventory cost reduction and operational improvements.
How Data Standardization Drives Inventory Cost Reduction
1. Elimination of Duplicate Materials
By identifying and removing duplicate SKUs, plants can:
- Reduce unnecessary purchases
- Free up storage space
- Lower carrying costs
Example: A chemical plant with 100,000 SKUs found a 12% duplication rate, leading to potential savings of $3.36 million.
2. Improved Inventory Visibility
With structured and categorized data, procurement teams gain better insights into:
- Stock levels
- Usage trends
- Reorder points
Benefit: Avoiding overstocking and stockouts, leading to inventory cost reduction and lower capital investment in excess inventory.
3. Optimized Procurement & Supplier Management
Standardized data enables procurement teams to:
- Negotiate better pricing by consolidating orders
- Reduce supplier redundancies
- Implement strategic sourcing practices
Impact: A fertilizer plant reduced its supplier base by 15%, cutting procurement costs by 8% and achieving significant inventory cost reduction.
4. Enhanced Material Classification & Grouping
Data standardization classifies materials based on industry standards, ensuring:
- Consistent naming conventions
- Easy material identification
- Efficient spare parts management
Result: Faster retrieval of materials, reduced downtime, and lower inventory costs.
5. Integration with ERP & MRO Systems
A clean and standardized Material Master seamlessly integrates with ERP (SAP, Oracle, Maximo) and MRO systems, allowing:
- Automated reorder processes
- Better inventory forecasting
- Reduced emergency purchases
Outcome: A chemical plant saw a 20% reduction in emergency orders, significantly lowering procurement expenses and contributing to inventory cost reduction.
Cost Reduction Potential: A Quick Overview
Key Area | Challenge | Data Standardization Benefit | Estimated Cost Savings |
---|---|---|---|
Duplicate Materials | Excess inventory and wasted capital | Elimination of redundant SKUs | 8-15% of inventory costs |
Procurement Inefficiencies | Unnecessary supplier redundancies | Consolidated purchasing power | 5-10% of procurement spend |
Overstocking & Stockouts | Poor inventory visibility | Optimized stock levels | 10-20% reduction in working capital |
Unplanned Downtime | Misidentified or unavailable spares | Improved material classification | 10-15% maintenance cost reduction |
ERP/MRO System Inefficiencies | Inaccurate data input | Automated, error-free data exchange | 5-10% reduction in admin costs |
How CODASOL Helps Fertilizer & Chemical Plants Achieve Inventory Cost Reduction
CODASOL’s AI/ML-driven Master Data Management (MDM) solutions ensure:
- End-to-end data standardization for material master records
- Duplicate identification & elimination using advanced algorithms
- Seamless ERP integration for real-time inventory tracking
- Automated data governance to maintain accuracy and compliance
By partnering with CODASOL, fertilizer and chemical plants can achieve rapid inventory cost reduction and optimization without disrupting existing operations.
Steps to Implement Data Standardization for Inventory Cost Reduction
- Conduct a Material Master Data Audit – Identify duplicates, inconsistencies, and outdated records.
- Develop Standard Naming Conventions – Align with industry standards (UNSPSC, ECCMA).
- Categorize & Group Materials – Use a hierarchical structure for easy identification.
- Integrate with ERP & MRO Systems – Ensure seamless data flow for procurement and inventory management.
- Train Employees on Data Governance – Establish policies to maintain data accuracy.
Are inventory inefficiencies costing your plant millions?
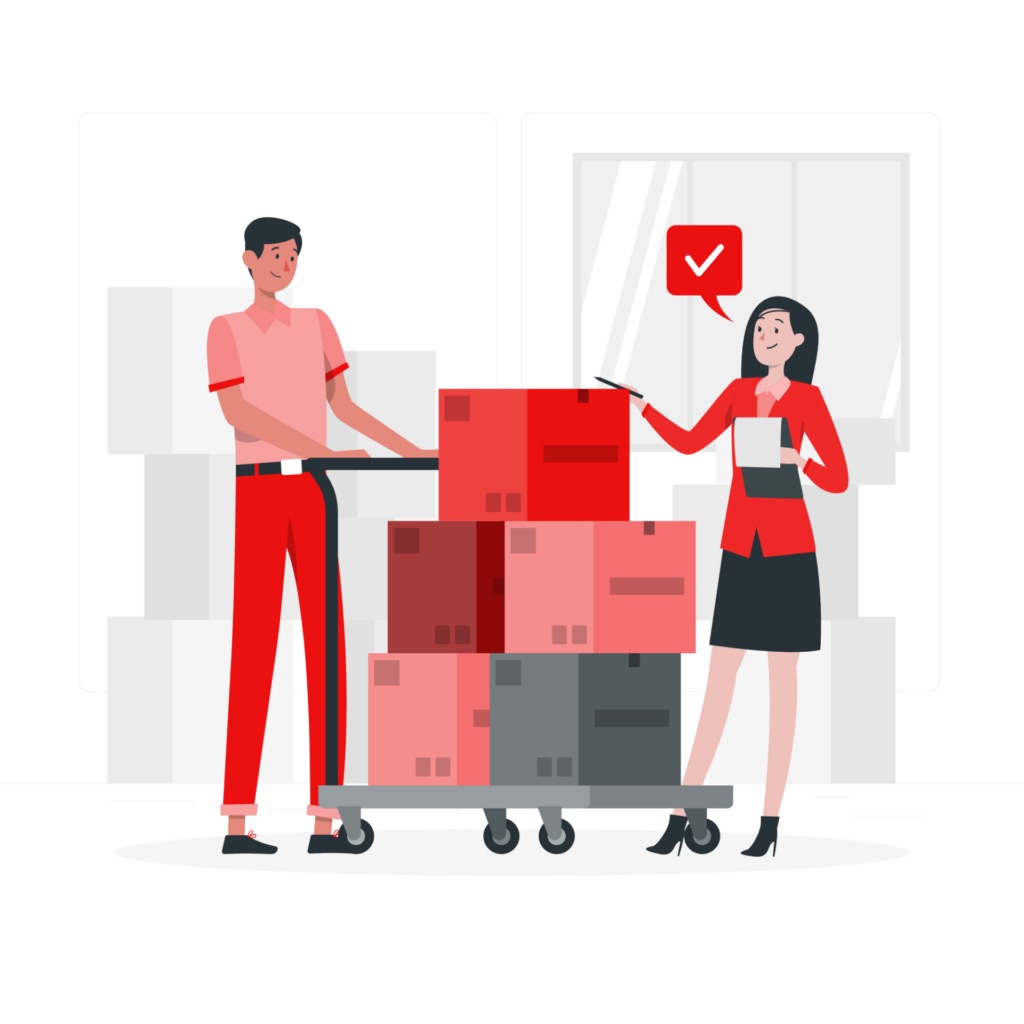
Contact us for a free consultation to assess your inventory challenges and discover the best strategy for inventory cost reduction.
FAQ: Inventory Cost Reduction with Data Standardization
1. What is data standardization in inventory management?
Data standardization involves structuring and organizing inventory data using consistent formats, naming conventions, and classifications to eliminate duplicates, improve accuracy, and optimize procurement.
2. How much can data standardization save a fertilizer or chemical plant?
Savings vary, but companies typically achieve inventory cost reduction of 10-20% and procurement expense reductions of 5-10% by eliminating duplicates, optimizing stock levels, and improving supplier management.
3. How long does it take to implement data standardization?
Implementation time depends on data complexity, but most companies achieve significant improvements within 3-6 months with the right tools and expertise.
4. Can data standardization work with existing ERP systems?
Yes, standardized inventory data seamlessly integrates with ERP systems like SAP, Oracle, and Maximo, enhancing automation and decision-making.
5. What is the first step in data standardization?
Start with a Material Master Data Audit to identify inconsistencies, duplicates, and outdated records. This lays the foundation for accurate, standardized inventory management and inventory cost reduction.
Final Thoughts
Fertilizer and chemical plants can significantly reduce inventory costs, optimize procurement, and improve operational efficiency with data standardization. By implementing these strategies with CODASOL, companies can enhance decision-making, streamline supply chains, and unlock hidden cost savings.
Looking to eliminate duplicate materials and optimize your procurement?
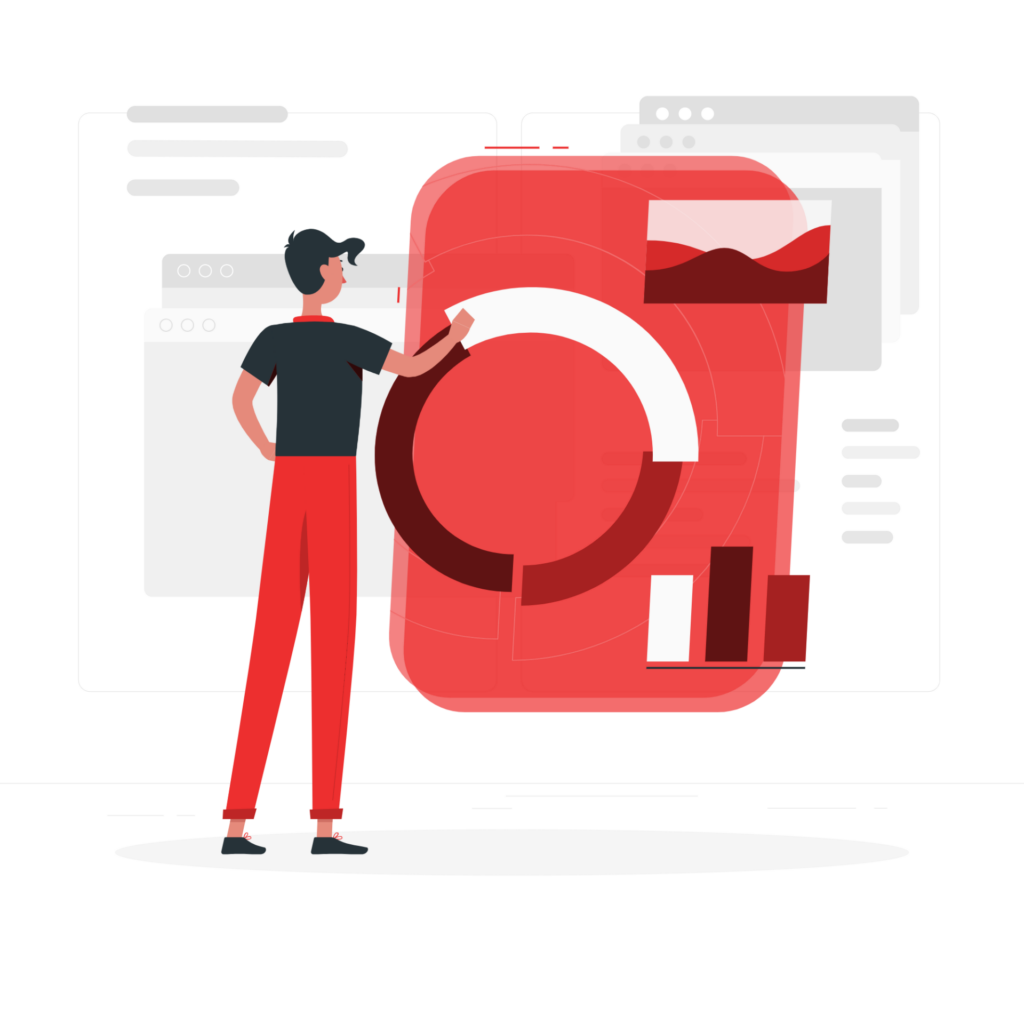