Procurement inefficiencies can cost businesses millions in unnecessary spending, supply chain delays, and excess inventory. One of the most effective ways to optimize procurement and reduce costs is material cataloguing, a systematic approach to organizing and standardizing material master data.
By implementing structured material cataloguing, businesses can eliminate duplicate purchases, improve supplier negotiations, and streamline procurement workflows. In this article, we’ll explore how material cataloguing enhances procurement efficiency and contributes to significant cost savings.
What Is Material Cataloguing?
Material cataloguing is the process of standardizing, organizing, and maintaining accurate data for all materials used within an organization. It involves:
- Data standardization: Ensuring uniform naming conventions, descriptions, and specifications.
- Deduplication: Identifying and removing duplicate entries to prevent redundant procurement.
- Categorization: Organizing materials into logical groups for easier searchability.
- Data enrichment: Adding critical attributes such as part numbers, manufacturer details, and sourcing information.
A well-structured material catalogue acts as a single source of truth for procurement teams, minimizing errors and inefficiencies in the supply chain.
How Material Cataloguing Optimizes Procurement
1. Eliminating Duplicate and Redundant Purchases
Duplicate materials in an organization’s master data often lead to unnecessary purchases, inflating procurement costs. Without proper cataloguing, the same item might be ordered under different names or codes, causing excess inventory buildup.
Solution: A well-structured material catalogue ensures that each item has a unique, standardized identifier, preventing duplication.
Case Study: Data Cleansing & De-duplication – A leading manufacturer reduced material duplication by 12%, saving $3.36 million in procurement costs.
2. Enhancing Supplier Negotiations & Cost Control
With standardized material cataloguing, businesses gain better visibility into procurement trends, spending patterns, and supplier pricing. This allows procurement teams to negotiate bulk discounts and optimize sourcing strategies.
Solution: A centralized material catalogue provides accurate data for price benchmarking, leading to better supplier agreements and reduced procurement costs.
Case Study: Material and Vendor Master Creation – A global company achieved 30% cost savings through improved supplier collaboration.
3. Improving Procurement Efficiency & Reducing Lead Times
Inefficient material data management slows down procurement cycles, leading to delays in production and increased carrying costs. A structured material catalogue streamlines the purchasing process, ensuring quick and accurate order placements.
Solution: By integrating material cataloguing with ERP systems like SAP or Oracle, companies can automate procurement workflows, reducing manual intervention.
Case Study: Material Data Management in SAP S/4 HANA – A leading enterprise reduced procurement lead times by 40% with structured material data.
4. Reducing Excess Inventory & Storage Costs
Poor material cataloguing often results in overstocking due to a lack of visibility into existing inventory. Businesses end up purchasing materials they already have, increasing storage costs and reducing working capital efficiency.
Solution: A well-organized material catalogue provides real-time inventory insights, preventing overstocking and minimizing obsolescence.
Case Study: Asset Registry Project – A global manufacturing firm reduced inventory holding costs by 20% through effective cataloguing.
5. Enabling Data-Driven Procurement Decisions
Accurate material cataloguing enhances spend analytics, allowing businesses to make informed procurement decisions. Companies can track consumption trends, supplier performance, and pricing variations to optimize procurement strategies.
Solution: AI-driven material cataloguing enables predictive analytics, helping procurement teams forecast demand and optimize purchase cycles.
Case Study: Coding & Cataloguing, BOM & Data Analytics Using AI/ML – A leading industrial firm optimized procurement using AI-driven cataloguing, reducing costs by 25%.
How Material Cataloguing Reduces Costs
Reduces Inventory Holding Costs
Better visibility into material data prevents overstocking and understocking, optimizing inventory levels and reducing carrying costs.
Minimizes Procurement Errors & Expedited Shipping Costs
Standardized material data ensures accurate order placements, eliminating costly expedited shipping fees due to incorrect or missing materials.
Improves Asset Utilization
By eliminating duplicate materials and improving data accuracy, companies maximize the usage of existing inventory before procuring new stock.
Procurement & Data Management Statistics:
- 12-15% of procurement budgets are lost due to poor material data quality. (Source: Industry Report)
- 75% of companies struggle with duplicate and inaccurate material data, leading to excess inventory and unplanned purchases. (Source: McKinsey)
- 80% of procurement professionals say inconsistent material descriptions create inefficiencies in sourcing and supplier negotiations. (Source: Deloitte)
- Standardized material cataloguing can reduce procurement costs by 5-15% and improve supplier management. (Source: Gartner)
- Companies implementing AI-driven material data management see an 18% faster procurement cycle and 40% lower lead times. (Source: Forrester)
Key Takeaway: Investing in structured material cataloguing leads to higher cost savings, better inventory control, and enhanced procurement efficiency.
🔗 Explore How Material Cataloging Supports Sustainability by Reducing Waste
Comparison: Without vs. With Material Cataloguing
Challenges Without Material Cataloguing | Benefits With Material Cataloguing |
---|---|
Duplicate purchases increase procurement costs. | Eliminates duplicate materials, reducing unnecessary spending. |
Inconsistent naming and descriptions lead to errors. | Standardized naming improves data accuracy. |
Procurement teams struggle to find materials quickly. | Easier searchability speeds up procurement cycles. |
Overstocking due to lack of visibility increases storage costs. | Real-time inventory insights prevent excessive stock. |
Poor supplier data leads to inefficient negotiations. | Better visibility enables stronger supplier agreements. |
Manual data entry errors disrupt procurement. | Integration with ERP/MDM automates processes, reducing errors. |
Implementing Material Cataloguing: Where to Start?
- Conduct a Material Data Audit – Assess the accuracy and completeness of existing data.
- Standardize Naming Conventions – Adopt industry standards (e.g., UNSPSC, NATO Codification).
- Use AI-Powered Deduplication Tools – Identify and eliminate duplicate material records.
- Integrate with ERP & MDM Systems – Ensure seamless data flow across procurement, inventory, and operations.
- Continuously Maintain Data Quality – Establish governance policies to keep the catalogue updated.
🔗 Read More: How Material Cataloging Supports Sustainability by Reducing Waste
Implementing Material Cataloguing with CODA: The Smarter Way
Material cataloguing can be overwhelming without the right tools. CODA, an AI-powered Master Data Management (MDM) platform, makes the process faster, more accurate, and cost-effective.
- Eliminates duplicate materials – AI-driven de-duplication cuts procurement waste and reduces costs.
- Standardizes material data – Ensures consistent naming, categorization, and descriptions across the organization.
- Integrates with ERP systems – Works seamlessly with SAP, Oracle, and Maximo for real-time procurement insights.
- Optimizes supplier data – Enhances vendor information, part numbers, and pricing details for better negotiations.
- Improves data governance – Keeps material records accurate, updated, and compliant with industry standards.
Real Results with CODA:
Companies using CODA’s Material Master Management solutions have achieved:
- Up to 15% procurement cost savings through better visibility and control.
- 40% faster procurement cycles by reducing manual errors and inefficiencies.
Material cataloguing isn’t just about cleaning up data, it’s about making smarter business decisions that cut costs, improve efficiency, and drive profitability. When you have a well-structured material catalogue, everything in procurement runs smoother.
With accurate, standardized data, companies can:
- Save 5-15% on procurement costs by eliminating duplicate purchases and optimizing sourcing.
- Speed up procurement cycles by reducing manual errors and ensuring fast, accurate order placements.
- Avoid excess inventory by knowing exactly what’s in stock before reordering.
- Strengthen vendor relationships with better pricing visibility and streamlined negotiations.
The bottom line? Better material data leads to better business outcomes. If procurement inefficiencies are draining your budget, material cataloguing is the fix.
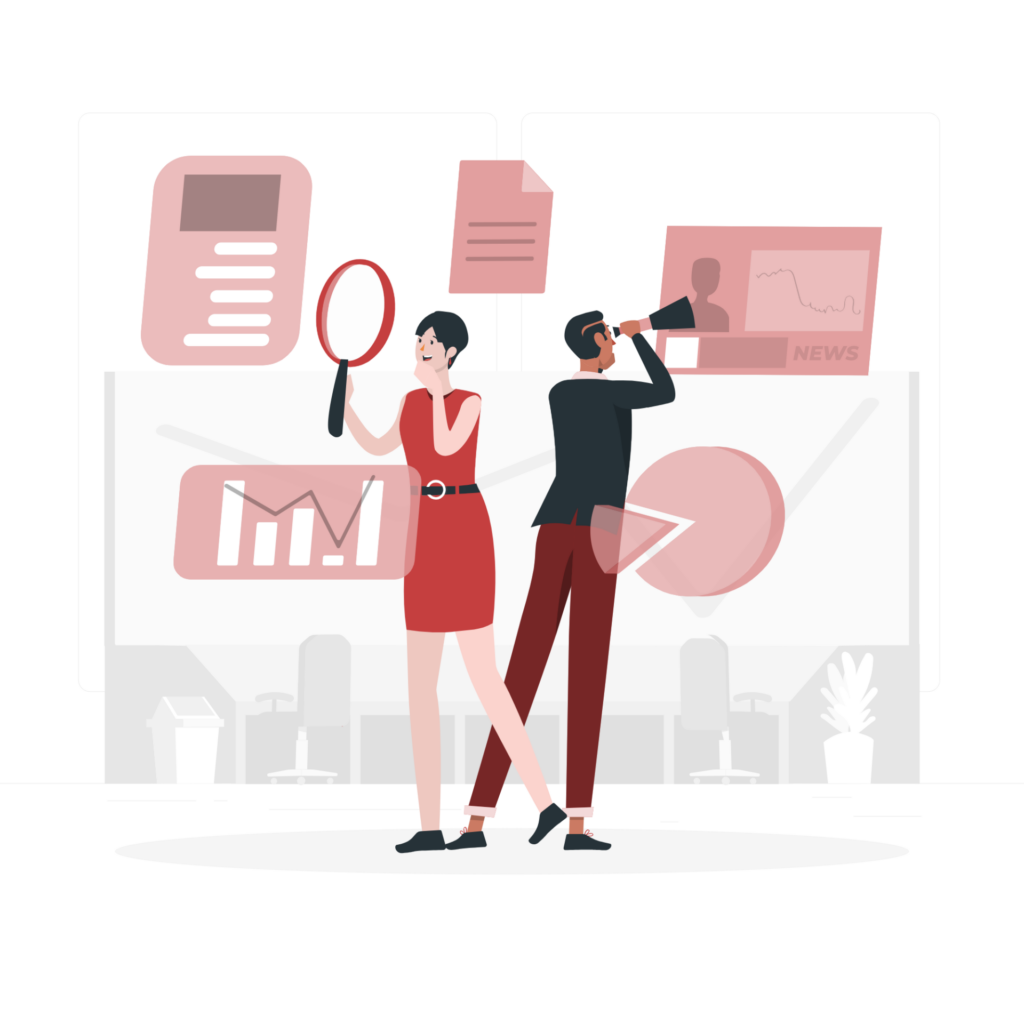
Ready to optimize your procurement?
Frequently Asked Questions (FAQs) on Material Cataloguing
1. What is material cataloguing in procurement?
Material cataloguing is the process of standardizing, organizing, and maintaining accurate material master data within an organization. It helps in eliminating duplicate purchases, optimizing inventory, and improving procurement efficiency.
2. How does material cataloguing reduce procurement costs?
By eliminating duplicate materials, improving supplier negotiations, and optimizing inventory management, material cataloguing helps businesses save 5-15% on procurement costs. It also reduces storage costs and prevents unnecessary purchases.
3. What are the key benefits of material cataloguing?
- Eliminates duplicate and redundant purchases
- Enhances supplier negotiations
- Reduces excess inventory and carrying costs
- Improves procurement efficiency and lead times
- Enables data-driven purchasing decisions
4. How does material cataloguing help in inventory management?
A well-structured material catalogue provides real-time visibility into stock levels, preventing overstocking and understocking. This helps businesses reduce excess inventory and improve working capital efficiency.
5. Can material cataloguing improve supplier negotiations?
Yes. Standardized material data allows procurement teams to benchmark pricing, track spending patterns, and negotiate better deals with suppliers, leading to significant cost savings.
6. What industries benefit from material cataloguing?
Industries like Oil & Gas, Manufacturing, Petrochemicals, Utilities, Steel, and Cement greatly benefit from material cataloguing as it enhances procurement efficiency and minimizes operational costs.
7. How does AI improve material cataloguing?
AI-powered cataloguing tools automate deduplication, categorize materials accurately, and provide predictive analytics to optimize procurement strategies.
8. What are the steps to implement material cataloguing?
- Conduct a material data audit
- Standardize naming conventions
- Use AI-driven deduplication tools
- Integrate with ERP & MDM systems
- Continuously maintain and update data quality
9. How does material cataloguing integrate with ERP systems?
Material cataloguing integrates with ERP platforms like SAP, Oracle, and Maximo to streamline procurement workflows, automate data entry, and improve accuracy in purchasing decisions.
10. What is the ROI of implementing material cataloguing?
Businesses that implement structured material cataloguing can achieve up to:
- 5-15% procurement cost savings
- 20-40% reduction in lead times
- 25% cost reduction using AI-driven cataloguing