Ensuring the longevity and optimal performance of industrial equipment is paramount for industries such as Oil & Gas, Utilities, Manufacturing, Real Estate & Construction, Marine & Ports, Healthcare & Lifesciences, Banking, Minerals & Metals, Government Entities, Defense, Engineering, Procurement, and Construction (EPC), and Aviation. Whether you’re in India, the GCC, or the Far East, applying reliability and inspection best practices is key to maximizing asset lifecycle, optimizing productivity, and reducing unplanned shutdowns.
Why Equipment Reliability Matters More Than Ever
Industrial assets are major capital investments. A single failure can lead to operational disruptions, safety hazards, or even regulatory penalties especially in high-stakes sectors like Defense, Marine & Ports, and Aviation. Increasing reliability through proactive reliability and inspection best practices not only saves costs but also strengthens your operational resilience.
Key Strategies for Enhancing Equipment Longevity
- Regular Equipment Inspections: Conducting routine inspections is crucial for early detection of potential issues. Regular assessments help identify wear and tear, misalignments, or other defects that could lead to equipment failure if left unaddressed.
- Implementing Preventive Maintenance Programs: Preventive maintenance involves scheduled servicing of equipment to prevent unexpected failures. This proactive approach includes tasks such as lubrication, part replacements, and system calibrations, ensuring equipment operates within optimal parameters.
- Utilizing Condition Monitoring Techniques: Condition monitoring entails tracking specific parameters like vibration, temperature, and pressure to detect anomalies indicative of potential failures. Techniques such as vibration analysis and thermal imaging enable maintenance teams to address issues before they escalate.
- Prioritizing Operator Training and Certification: Ensuring that equipment operators are adequately trained and certified reduces the risk of human error, which can lead to equipment damage. Continuous education on the latest operational procedures and safety protocols is essential.
- Adopting Risk-Based Inspection (RBI) Approaches: RBI focuses on assessing the likelihood and consequences of equipment failure, allowing for prioritized inspection efforts. This method ensures that resources are allocated effectively to areas with the highest risk.
- Ensuring Proper Equipment Storage and Handling: Proper storage conditions, including controlled environments and protection from contaminants, play a significant role in extending equipment lifespan. Adhering to manufacturer guidelines for storage and handling prevents premature deterioration.
- Maintaining Accurate Maintenance Records: Documenting all maintenance activities provides valuable data for tracking equipment performance over time. These records aid in identifying recurring issues and formulating strategies for continuous improvement.
- Utilizing Original Equipment Manufacturer (OEM) Parts: When replacements are necessary, using OEM parts ensures compatibility and maintains the integrity of the equipment. OEM parts are designed to meet the original specifications, thereby preserving performance standards.
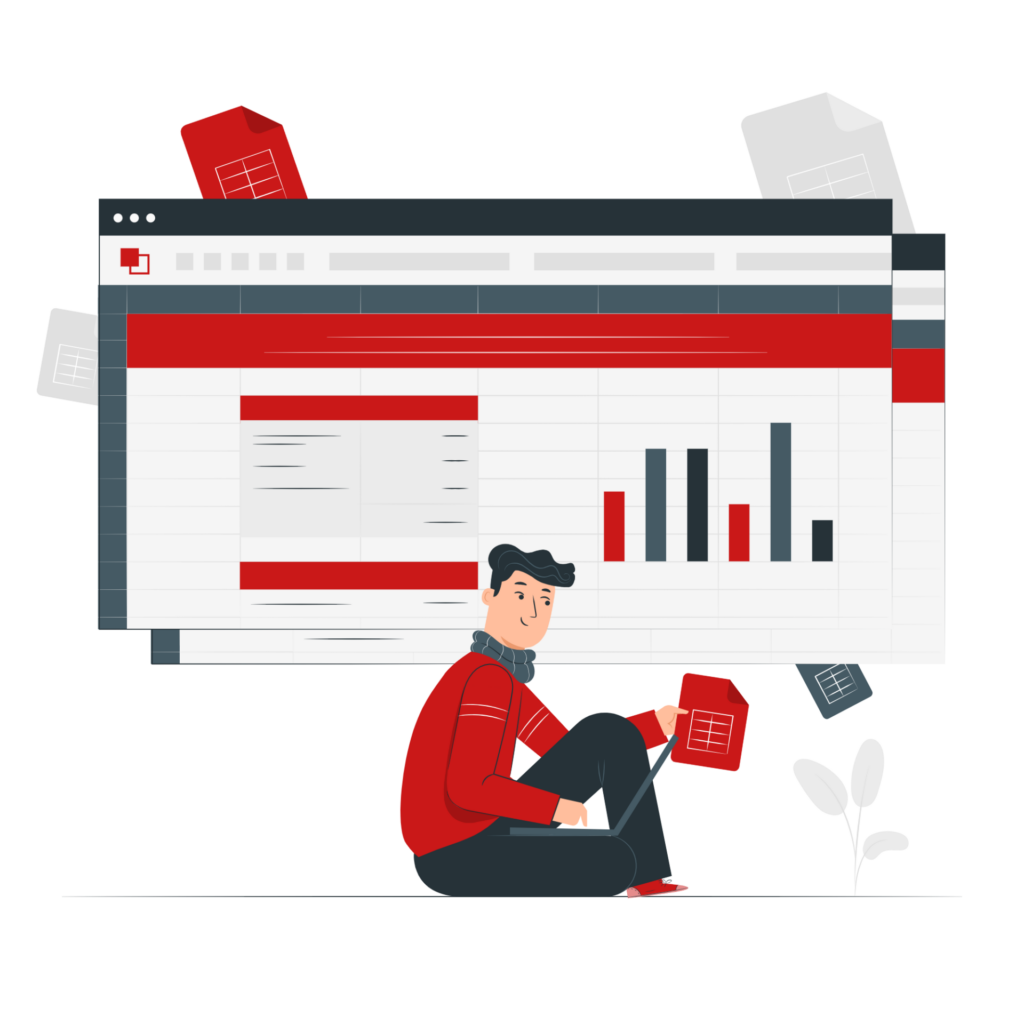
Want to audit your current asset strategy?
Download our free “Industrial Equipment Reliability Checklist”
Top Reliability and Inspection Best Practices
1. Adopt a Risk-Based Inspection (RBI) Strategy
RBI allows organizations to focus their inspection efforts where they are most needed—on equipment with the highest risk of failure. This methodology is particularly useful in Oil & Gas, Refineries, and Chemical plants, where safety and cost control are critical.
2. Implement Condition-Based Monitoring (CBM)
CBM uses real-time data from sensors to assess the health of machinery. Industries in Manufacturing and Healthcare benefit from CBM by anticipating failures before they occur, minimizing unplanned outages.
3. Create a Centralized Asset Register
A complete, digitized asset inventory ensures traceability of every maintenance activity and aids in performance analysis. This is vital for large-scale operations in Construction, Mining, and Government Entities.
4. Standardize Inspection Procedures
Standard Operating Procedures (SOPs) for inspections create uniformity and accuracy across teams. Consistency is especially important for global operations in Banking, Real Estate, or Multinational EPCs.
5. Train and Certify Inspectors
Human error is one of the leading causes of equipment failures. Invest in regular training and certification programs, particularly in regulated sectors like Defense and Aviation, to ensure compliance and competency.
6. Use Predictive Maintenance Algorithms
AI and Machine Learning can forecast potential failures by analyzing historical and sensor data. This is transforming how organizations in GCC and Far East are managing their critical infrastructure.
7. Establish Failure Mode and Effects Analysis (FMEA)
FMEA helps prioritize maintenance tasks by identifying the severity and probability of equipment failure modes. It’s a must-have framework for sectors like Utilities, Marine, and EPC.
Advanced Techniques in Equipment Reliability
Predictive Maintenance
Predictive maintenance evaluates the condition of equipment by performing periodic (offline) or continuous (online) equipment condition monitoring. The ultimate goal of this approach is to perform maintenance at a scheduled point in time when the maintenance activity is most cost-effective and before the equipment loses performance within a threshold. This results in a reduction in unplanned downtime costs because of failure, where costs can be substantial depending on the industry. Predictive maintenance techniques include vibration analysis, thermography, and ultrasonic testing.
Reliability-Centered Maintenance (RCM)
Reliability-Centered Maintenance is a process used to determine the maintenance requirements of physical assets in their operating context. It seeks to optimize the maintenance strategy by balancing cost and reliability. RCM involves identifying the functions of the equipment, the ways it can fail, and prioritizing the maintenance tasks to mitigate those failures.
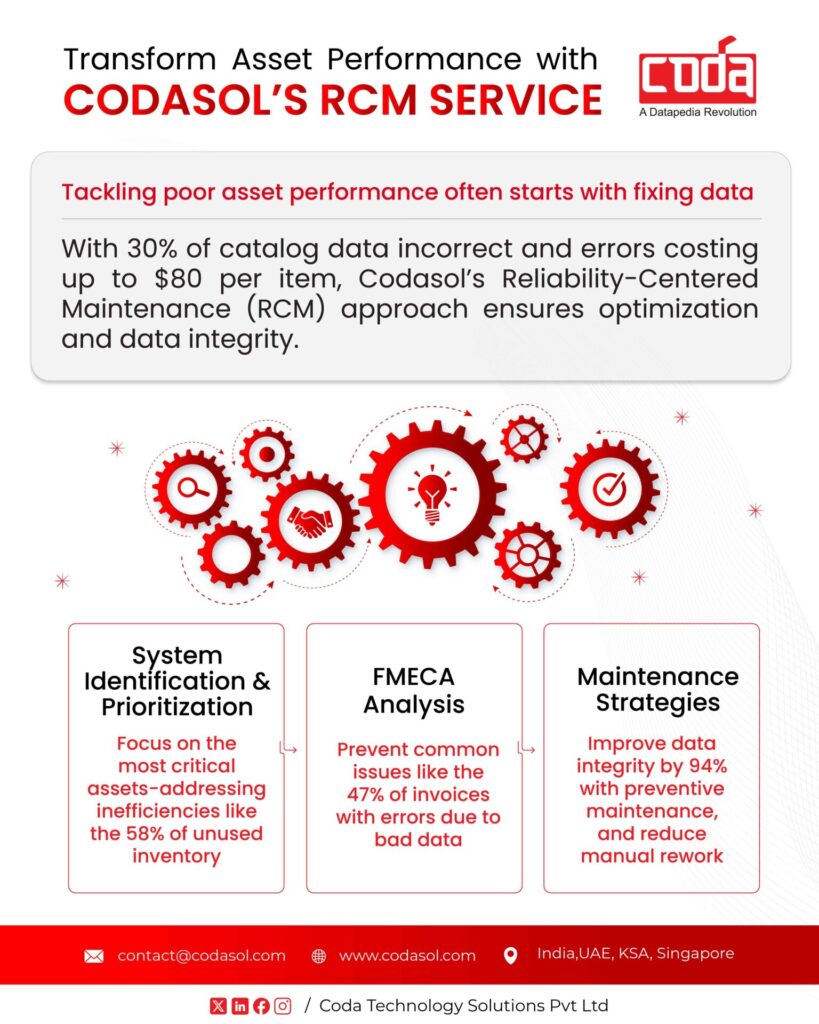
Non-Destructive Testing (NDT)
Non-Destructive Testing encompasses a range of techniques used to evaluate the properties of a material, component, or system without causing damage. Common NDT methods include ultrasonic testing, radiographic testing, magnetic particle testing, and dye penetrant testing. These techniques are essential for detecting internal and surface defects in equipment.
Comparison of Maintenance Strategies
Maintenance Strategy | Description | Best For | Cost Efficiency | Risk Level |
---|---|---|---|---|
Reactive Maintenance | Fix after failure | Small operations | Low (short-term) | High |
Preventive Maintenance | Scheduled servicing | Utilities, Manufacturing | Moderate | Medium |
Predictive Maintenance | Data-driven forecasting | Oil & Gas, Aviation, Healthcare | High (long-term ROI) | Low |
Risk-Based Inspection (RBI) | Prioritize based on asset criticality and failure impact | EPC, Defense, Real Estate | High | Low |
Condition-Based Monitoring | Real-time sensor-based monitoring | Marine, Banking, Government | High | Very Low |
Industry-Specific Insights on reliability and inspection best practices
Oil & Gas
With high-value assets like compressors and pipelines, RBI and real-time monitoring can prevent catastrophic failures.
Manufacturing
Standardizing SOPs and deploying condition-monitoring devices can reduce scrap and downtime.
Real Estate & Construction
Focusing on HVAC and elevator inspections ensures tenant satisfaction and lowers repair costs.
Marine & Ports
Regular hull inspections and CBM reduce drydock time and extend vessel service life.
Healthcare
Medical devices need periodic inspection and predictive analytics to ensure patient safety and avoid litigation.
Government & Defense
Ensuring asset reliability protects mission readiness and national infrastructure.
Frequently Asked Questions (FAQs)
1. What is the difference between preventive and predictive maintenance?
Preventive maintenance follows a fixed schedule regardless of equipment condition, while predictive maintenance uses data to determine the optimal time for service based on real-time asset health.
2. How often should industrial inspections be performed?
It depends on the asset type and risk profile. High-risk equipment in Oil & Gas may need monthly or even real-time monitoring, while others might require quarterly reviews.
3. Is investing in inspection technology worth it for SMEs?
Absolutely. With affordable sensor-based systems and cloud-based analytics, even small to mid-sized firms can reap the benefits of improved uptime and lower maintenance costs.
4. How can AI improve equipment reliability?
AI can detect patterns in equipment behavior that precede failure. It allows companies to act before a breakdown occurs, reducing both downtime and repair costs.
5. What’s the first step to improving reliability?
Start by conducting a comprehensive audit of your existing asset base, maintenance records, and failure history. This forms the foundation for any reliability improvement plan.
Need help building a reliability framework?
Request a free consultation with our experts on how to implement risk-based inspection and predictive maintenance for your industry.
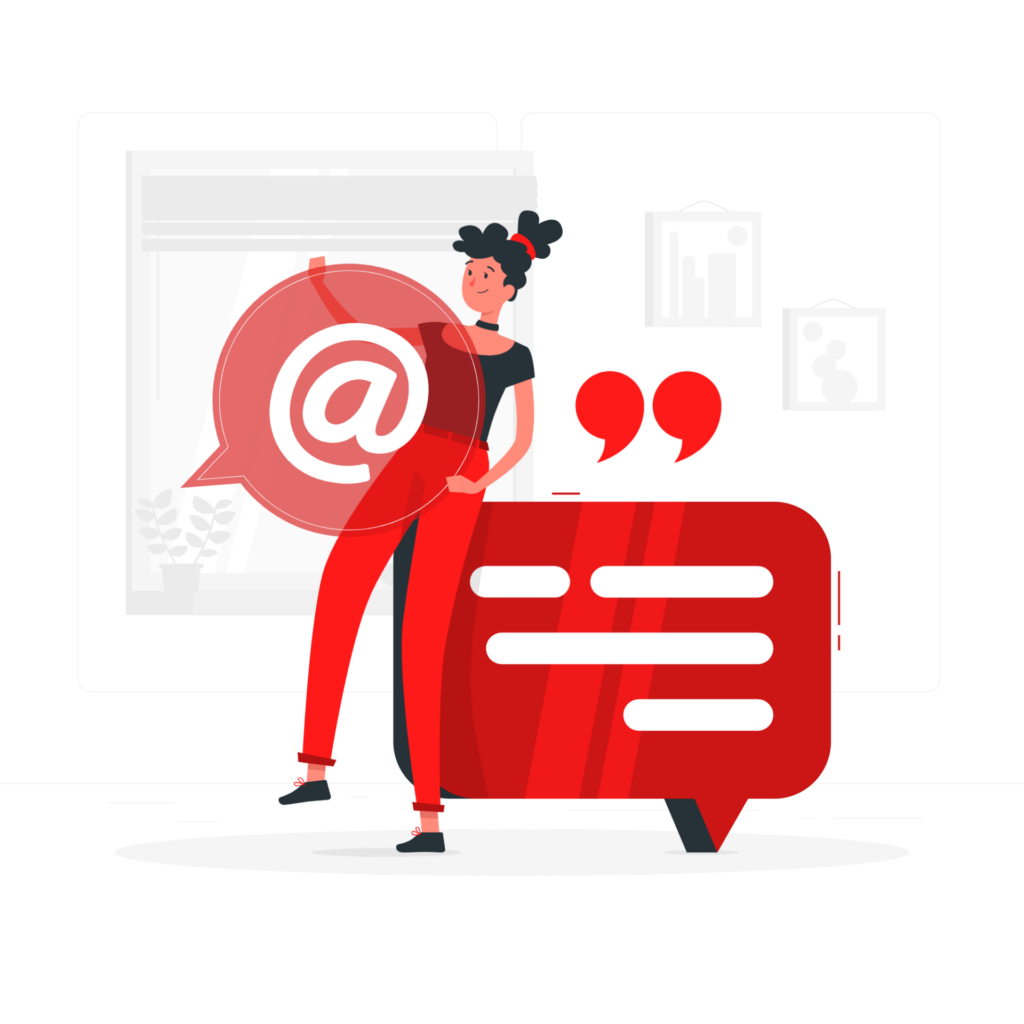