One powerful yet underutilized solution is the Spare Parts Interchangeability Record (SPIR)—a structured approach that helps businesses optimize spare parts procurement, reduce downtime, and improve operational efficiency.
Unplanned downtime and supply chain disruptions are two of the biggest threats to industrial operations, causing millions in lost revenue annually. Organizations struggle with spare parts availability, procurement inefficiencies, and data inconsistencies, leading to major revenue losses.
In industries such as Oil & Gas, Petrochemicals, Manufacturing, and Power Generation, unplanned downtime due to equipment failure can cost millions in lost production and emergency maintenance. Despite this, many companies still struggle with inefficient spare parts management, leading to procurement delays, excess inventory, and mismatches.
In this in-depth guide, we’ll explore:
- What SPIR is and why it is essential for asset-heavy industries
- Key benefits of SPIR and how it helps reduce operational costs
- Case studies demonstrating SPIR’s real-world impact
- Common challenges in SPIR implementation and how to overcome them
- A step-by-step approach to implementing SPIR successfully
Let’s dive in.
What is SPIR (Spare Parts Interchangeability Record)?
The Spare Parts Interchangeability Record (SPIR) is a comprehensive document used in procurement and inventory management to standardize spare parts data across multiple equipment units. It helps organizations identify interchangeable parts, optimize procurement, and prevent unnecessary stockpiling.
Key Elements of a SPIR Document
- Spare part specifications – Material, dimensions, compatibility
- Manufacturer details – OEM, supplier data, and part codes
- Interchangeability information – Equipment compatibility and alternatives
- Recommended stock levels – Based on consumption history and criticality
By leveraging SPIR, companies eliminate procurement inefficiencies, reduce inventory costs, and ensure that critical spares are always available.
Why Traditional Spare Parts Management Fails
- Duplicate and obsolete parts increase inventory carrying costs
- Unnecessary stockpiling due to poor demand forecasting
- Procurement delays when critical spares are not cataloged properly
- Mismatch issues when incorrect parts are used, leading to maintenance failures
SPIR provides a single source of truth for spare parts management, eliminating these inefficiencies.
Key Benefits of SPIR Implementation
1. Reduces Spare Parts Inventory Costs by 20-30%
- Eliminates duplicate and non-standardized parts
- Prevents overstocking through demand-based stock optimization
- Enables bulk procurement discounts by standardizing parts
Example: A petrochemical company reduced inventory costs by 25% ($3.2 million) by implementing SPIR-based spare parts optimization.
2. Prevents Unplanned Downtime and Revenue Loss
- Ensures critical spare parts are readily available
- Reduces maintenance delays caused by missing or incorrect parts
- Enables predictive maintenance with real-time spare part availability
Example: An offshore oil platform prevented 12 hours of downtime, saving $8.9 million in lost production, by using SPIR for efficient spare parts management.
3. Enhances Supply Chain Efficiency
- Standardizes parts across multiple assets, reducing supplier dependency
- Improves lead time predictability for spare parts procurement
- Enables faster RFQs and vendor negotiations
Example: A steel manufacturer cut procurement lead time by 40%, improving maintenance efficiency.
4. Strengthens Data Accuracy & Compliance
- Reduces manual errors in spare parts classification
- Ensures ERP and MRO system data consistency
- Supports compliance with ISO 55000 (Asset Management) & industry standards
Example: A cement plant improved data accuracy by 92%, preventing spare parts mismatches and maintenance failures.
5. Improves Decision-Making with AI & Data Analytics
- Enables AI-driven inventory optimization
- Facilitates spare parts lifecycle tracking
- Provides insights into failure rates and spare part consumption trends
🔗 Related read: Why Master Data Management is Critical for Supply Chains
The Cost of Downtime and Supply Chain Delays
Unplanned downtime costs businesses up to $260,000 per hour in industries like oil & gas, petrochemicals, and manufacturing. The primary causes?
- Inefficient spare parts management
- Lack of accurate BOM (Bill of Materials)
- Delayed procurement cycles
- Inconsistent material master data
SPIR is a proven strategy to prevent downtime and supply chain delays. Without a structured SPIR, maintenance teams struggle to find the right spare parts in emergencies. This leads to longer turnaround times and significant revenue losses.
By standardizing spare parts data, optimizing inventory, and leveraging AI-driven BOM analytics, businesses can cut costs, boost efficiency, and enhance operational resilience.
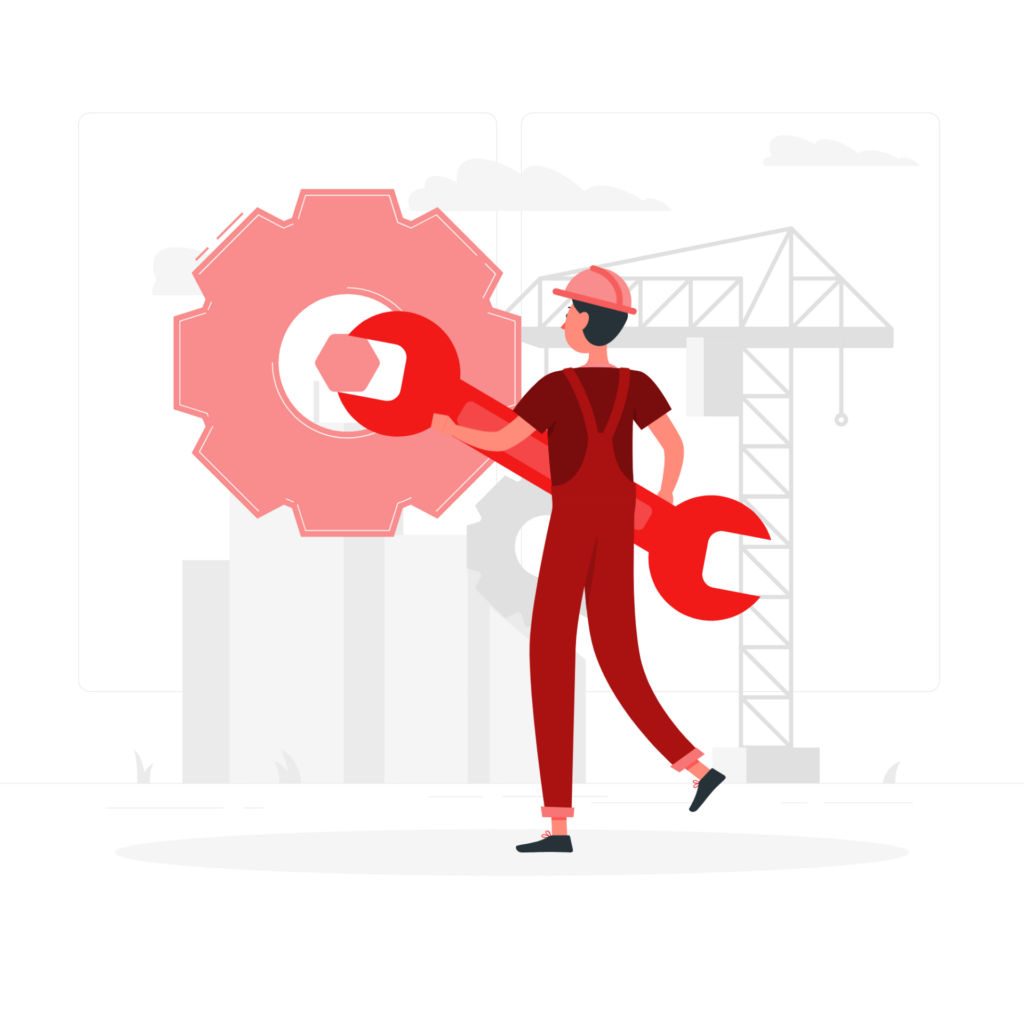
Want to prevent unplanned downtime? Book a Free Consultation with Our Experts!
Real-World Case Studies: SPIR in Action
Case Study 1: BOM Creation and PM Plan in SAP
A leading chemical manufacturing company faced frequent downtime due to missing spare parts in their inventory. CODASOL implemented BOM creation and preventive maintenance (PM) planning in SAP, enabling them to:
- Reduce maintenance delays by 40%
- Eliminate duplicate spare parts procurement
- Improve asset reliability with proactive maintenance
🔗 Read the full case study: BOM Creation and PM Plan in SAP
How SPIR Prevents Downtime & Supply Chain Delays
1. Ensuring Spare Parts Availability
SPIR provides a centralized database of interchangeable spare parts, helping procurement teams quickly identify alternatives when primary parts are unavailable. This minimizes supply chain delays and ensures smooth operations.
2. Optimizing BOM and Inventory Management
SPIR enables accurate Bill of Materials (BOM) creation, ensuring every spare part is linked to the right equipment. AI-driven material master standardization further reduces errors in spare parts procurement.
🔗 Learn more: Master Data Management in the Supply Chain
3. AI & ML for Spare Parts Standardization
Using AI/ML-powered cataloging and classification, businesses can:
- Eliminate data duplication in spare parts inventory
- Improve spare parts searchability
- Reduce procurement lead times by 30%
Bonus: Get a Free SPIR Audit for Your Business!
Identify gaps in your spare parts inventory and BOM data with a FREE SPIR ASSESSMENT from CODASOL.
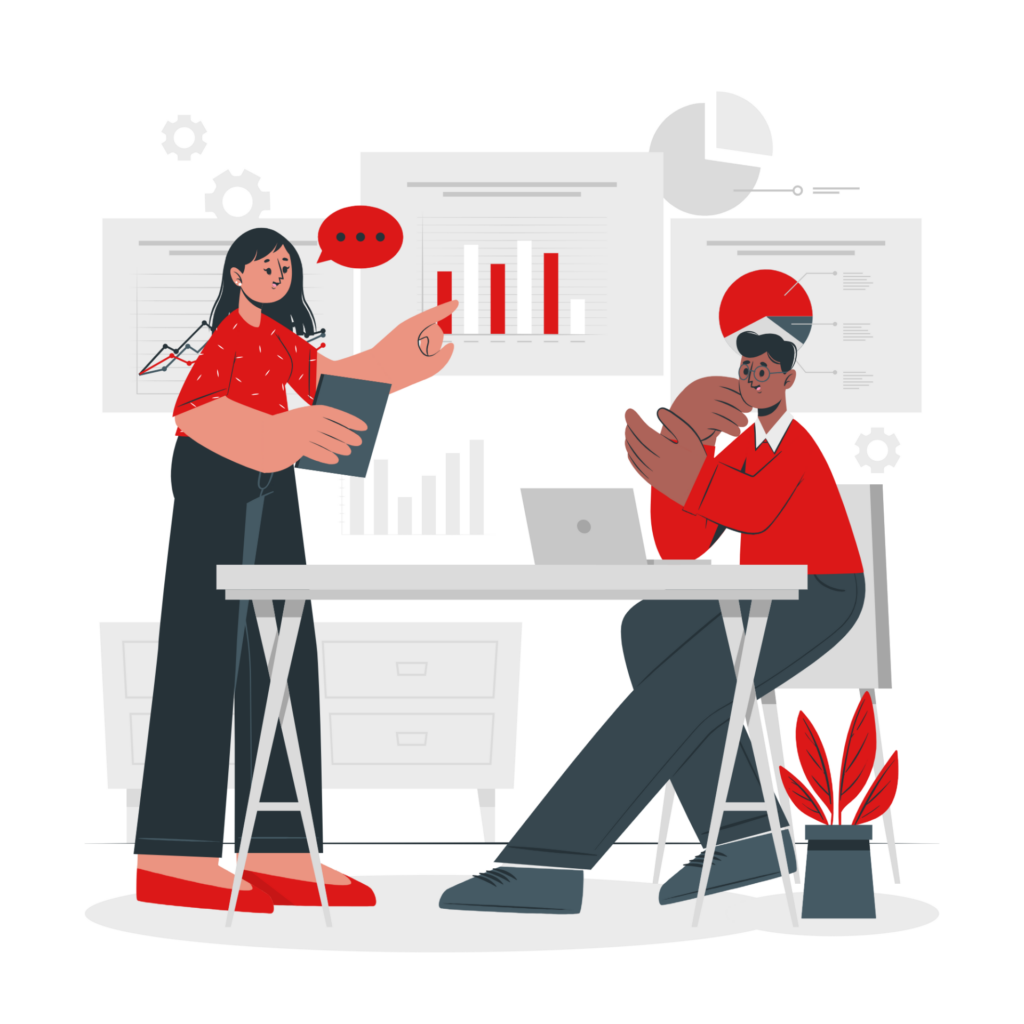
Case Study 2: AI/ML-Based Cataloging & BOM Analytics
A global petrochemical company struggled with spare parts duplication and inconsistent material coding. CODASOL implemented AI-powered cataloging and BOM analytics, achieving:
- 15% cost savings on spare parts procurement
- 50% reduction in duplicate spare parts
- Improved data accuracy and operational efficiency
🔗 Read the full case study: AI/ML-Based Cataloging & BOM Analytics
How to Implement SPIR for Maximum Impact
1. Standardize Your Material Master Data
Duplicate and inconsistent data can cause spare parts procurement inefficiencies. Material master standardization ensures accurate descriptions, classifications, and specifications.
🔗 Related read: Top 10 Best Practices for Data Cleansing and Standardization
2. Leverage AI-Driven Data Management
AI-based Master Data Management (MDM) helps businesses create an optimized spare parts database, reducing unplanned shutdown costs by $8.9M for oil & gas companies.
🔗 Read how: How MDM Saves Oil & Gas Companies $8.9M in Unplanned Shutdown Costs
3. Integrate SPIR with Your ERP System
Seamless integration with SAP, Oracle, and Maximo enhances data visibility, ensuring maintenance teams access the right spare parts at the right time.
🔗 Explore more: SAP Master Data Management: A Complete Guide
How to Implement SPIR: A Step-by-Step Checklist
- Step 1: Conduct a spare parts audit to identify duplicates and obsolete parts
- Step 2: Standardize spare parts naming conventions & classifications
- Step 3: Implement a Master Data Management (MDM) system to centralize SPIR data
- Step 4: Integrate SPIR with ERP, CMMS, and MRO procurement workflows
- Step 5: Train procurement, maintenance, and supply chain teams on SPIR usage
- Step 6: Continuously monitor spare parts demand & optimize procurement
Companies using AI-driven MDM platforms like PROSOL see 20-30% faster SPIR implementation and inventory savings
Common Challenges in SPIR Implementation (And How to Overcome Them)
1. Data Inconsistencies & Duplicate Records
Solution: Conduct a data cleansing exercise before SPIR implementation. AI-driven MDM solutions (like PROSOL) help standardize spare parts data.
2. Resistance to Change from Maintenance & Procurement Teams
Solution: Provide SPIR training, share real-world success stories, and ensure gradual adoption.
3. Integration Issues with Existing ERP/MRO Systems
Solution: Use API-based integration with ERPs like SAP, Oracle, and Maximo to ensure seamless data flow.
4. Lack of Vendor Collaboration
Solution: Implement vendor-managed inventory (VMI) contracts based on SPIR recommendations.
SPIR vs. Traditional Spare Parts Management
Feature | Traditional Spare Parts Management | SPIR-Driven Spare Parts Management |
---|---|---|
Inventory Control | Reactive (excess stock or shortages) | Proactive (optimized stock levels) |
Procurement Lead Time | High (last-minute orders) | Lower (standardized supplier data) |
Downtime Impact | Frequent delays | Reduced downtime with ready availability |
Cost Savings | Minimal | 15-30% savings on inventory |
ERP Integration | Manual, error-prone | Automated, data-driven |
→ With SPIR, companies achieve cost savings, improved asset reliability, and operational efficiency.
Final Thoughts: Why SPIR is a Must-Have for Asset-Intensive Industries
- Reduces spare parts costs by up to 30%
- Prevents costly unplanned downtime
- Improves procurement efficiency & supply chain transparency
- Strengthens asset reliability & maintenance planning
Next Steps:
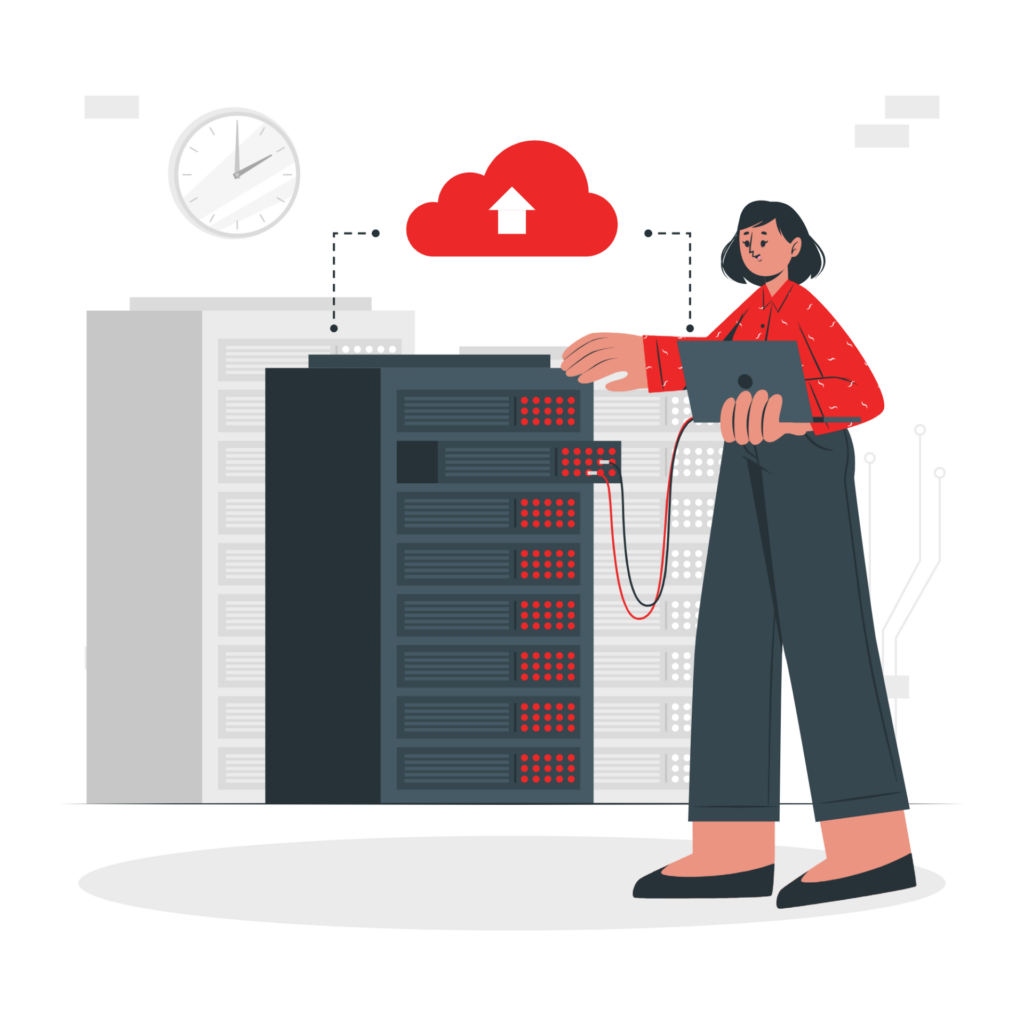
Want to optimize your spare parts strategy?
Explore how MDM can transform inventory management → Read our guide on Master Data Management