In the fast-paced and demanding environment of cement plants, maintaining smooth operations is critical to meeting production goals. Preventive maintenance is a proven strategy that helps avoid downtime, maximize asset life, and ensure efficiency. By proactively maintaining key equipment, cement plants can mitigate the risk of unexpected failures and reduce costly repairs.
What is a Preventive Maintenance Plan?
A preventive maintenance plan outlines specific actions to prevent equipment failures, minimize downtime, and maintain optimal performance. It involves proactive measures taken while equipment is operational to reduce the likelihood of failures.
This approach focuses on critical equipment such as rotary kilns, crushers, mills, conveyors, and hydraulic systems in industries like cement. Implementing an efficient preventive maintenance program reduces downtime, extends asset life, and enhances operational efficiency.
Why Preventive Maintenance Matters in Cement Plants
Equipment must operate continuously and reliably to produce high-quality cement. Unplanned downtime in even one machine can disrupt operations, compromising quality, efficiency, and safety. Monitoring motors, conveyors, fans, blowers, and gearboxes is vital to prevent such scenarios.
Key Benefits of Preventive Maintenance Plan in Cement Plants
1. Enhanced Safety
Regular maintenance reduces risks in hazardous environments by ensuring equipment operates reliably and scheduling safety checks to prevent accidents.
2. Extended Equipment Lifespan
Cement plant equipment is made with longevity and durability in mind. Routine servicing minimizes wear and tear, prolonging the life of machinery and lowering long-term costs.
3. Minimized Downtime
Scheduled maintenance prevents unexpected failures, ensuring consistent productivity and reducing disruptions.
4. Energy Efficiency
Well-maintained machines consume less energy, cutting costs and supporting sustainability goals. A preventive plan ensures safety, streamlined efficient operations, long-lasting assets, and improved cost management.
How to Create an Effective Maintenance Plan
Follow these steps to establish a robust preventive maintenance plan:
- Assess Your Inventory: Catalog all assets and prioritize based on criticality.
- Identify Maintenance Tasks and Triggers: Define tasks and specify the conditions that trigger maintenance.
- Create Itemized Task Lists: Ensure accurate execution of each task.
- Equip and Record: Identify tools needed for execution and maintain detailed records.
- Activate the Plan: Implement and monitor the preventive maintenance program.
Process of Preventive Maintenance in Cement Plants
Real-Time Monitoring
Use triaxial vibration analysis, which measures an object’s vibrations and motion or oscillations in three dimensions, typically in the X, Y, and Z axes, to predict the pattern of movements.
Scheduled Predictive Maintenance
Plan actions like centrifuging, oil replacement, and gearbox inspections to prevent failures.
Timely Alerts
Alerts via email or SMS provide instant updates on unusual patterns or potential risks, enabling quick intervention to mitigate equipment damage.
Data-Driven Decision-Making
Weekly insights generated from monitoring systems and maintenance logs provide actionable information. These insights allow maintenance teams to prioritize urgent tasks and plan resources effectively.
6 Key Steps to Avoid Downtime in Cement Plants
- Inspection and Monitoring
Regular checks of equipment like crushers, mills, rotary kilns, and conveyors are crucial. Use condition-monitoring tools such as vibration analysis, thermography, and oil analysis to detect potential issues early.
- Lubrication Management
Based on the manufacturer’s recommendation, lubrication for rotating machinery is scheduled at regular time intervals to reduce the chances of wear and tear.
- Scheduled Cleaning
Routine cleaning removes dust, clinker, and residues that can cause blockages or overheating. Maintain adequate airflow in dust collectors and baghouses.
- Component Replacements
Replace wear parts, such as grinding media, kiln linings, and filter bags, promptly to prevent catastrophic failures.
- Calibration and Alignment
Align parts, belts, rollers, and other components precisely. Regularly calibrate instruments like pressure gauges, flow meters, and temperature sensors.
- Documentation and Planning
Keep comprehensive records of maintenance activities and equipment performance for future reference and schedule turnaround maintenance to minimize disruptions to boost production.
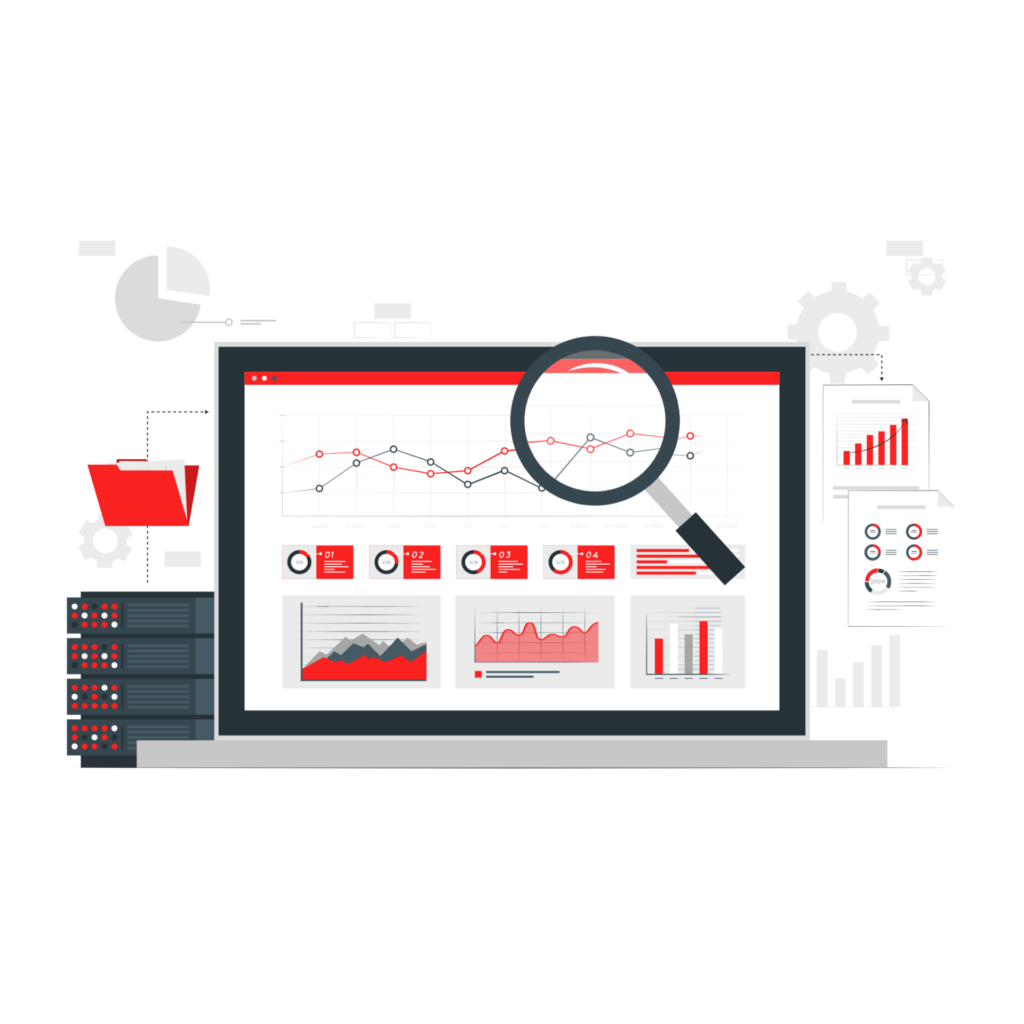
Proactively tackle maintenance challenges with CODA’s expert-designed preventive maintenance plans.
How Coda Offers Maintenance Strategies
CODA provides expert maintenance strategies tailored to the unique needs of cement plants. Here’s how we help optimize maintenance operations:
Preventive Maintenance (PM) Plan Development
We work closely with cement plants to design customized preventive maintenance plans. These plans outline specific maintenance tasks, their frequencies, and the necessary materials, ensuring a systematic approach to upkeep.
Detailed Task List Creation
CODA creates clear and detailed task lists to help technicians perform maintenance efficiently and with precision, reducing errors and enhancing productivity.
Reliability-Centered Maintenance (RCM)
Our RCM approach analyzes equipment functions, potential failure modes, and their impacts to develop targeted maintenance plans. Our simplified RCM process prioritizes critical failure modes, ensuring reliability strategies are cost-effective and impactful.
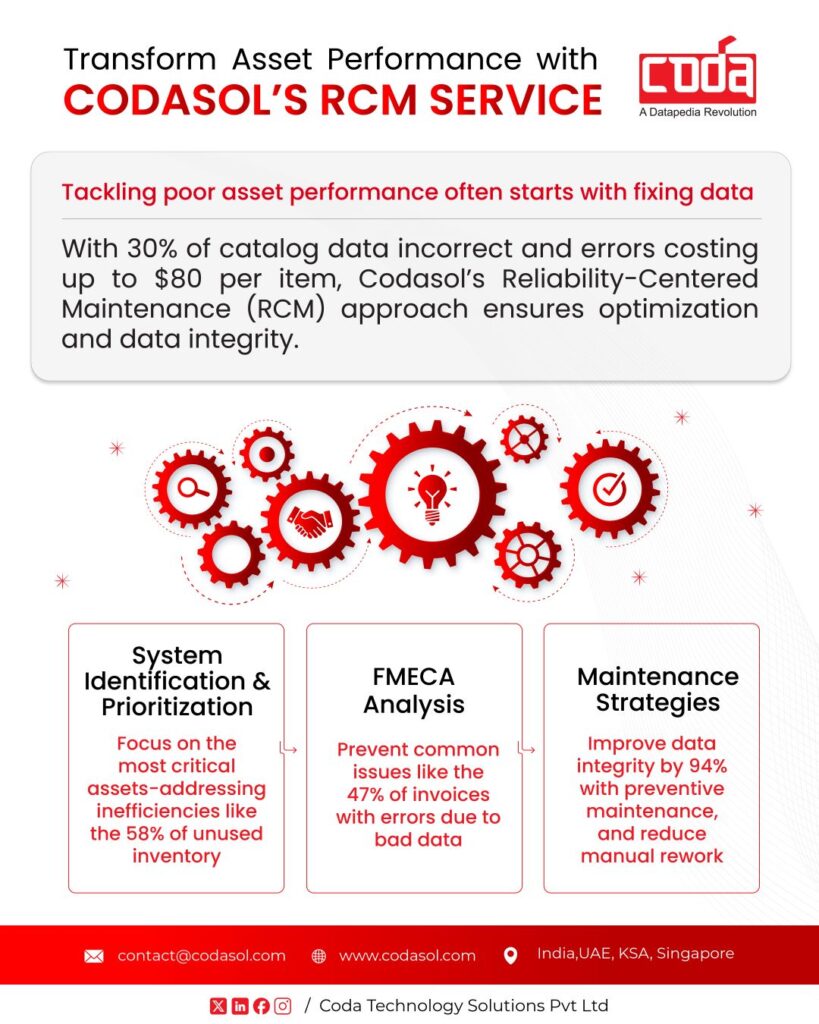
Wrapping Thoughts
Implementing an effective preventive maintenance plan is essential for cement plants looking to enhance safety, extend equipment life, and improve operational efficiency. With CODA’s expert strategies and data-driven insights, cement plants can reduce downtime, cut maintenance costs, and increase overall productivity.
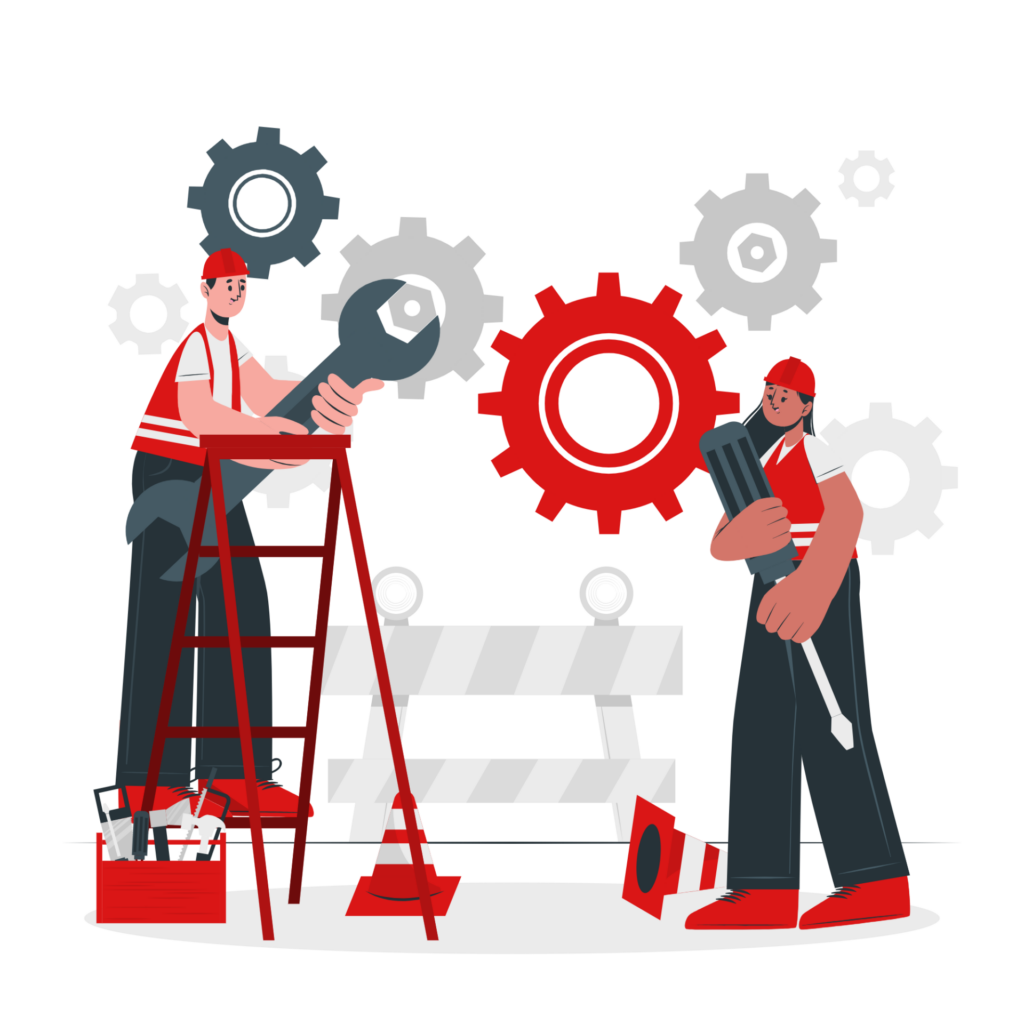
Create a tailored preventive plan with us.
Ready to transform your maintenance strategy?